Rivets are mechanical fasteners used to join two or more metal sheets together in a secure and permanent manner. They provide a strong and reliable connection, distributing the load across the joined sheets. Rivets are widely used in various industries for metal sheet assembly due to their strength, versatility, and ease of installation.Rivets are widely used in metal sheet assembly to provide a strong, secure, and permanent fastening method. Here are seven common types of rivets used for metal sheet assembly:
Solid Rivets:
Solid rivets are a traditional type of rivet and consist of a solid shaft with a head on one end.
They require access to both sides of the assembly for installation and provide excellent strength and reliability.
Blind Rivets (Pop Rivets):
Blind rivets, also known as pop rivets, are widely used when access is limited to one side of the assembly.
They feature a hollow body and a mandrel (stem) that breaks off during installation to securely clamp the sheets together.
Semi-Tubular Rivets:
Semi-tubular rivets have a partially hollow shaft and a head on one end.
They are installed using a rivet press and are commonly used in applications requiring a lower-cost alternative to solid rivets.
Tubular Rivets:
Tubular rivets are similar to semi-tubular rivets but have a completely hollow shaft.
They are lightweight and ideal for applications where weight reduction is important.
Tri-Fold Rivets:
Tri-fold rivets, also known as triple-leg rivets, have three legs that fold out when the mandrel is pulled during installation.
They provide excellent strength and are often used in applications where a high-strength connection is required.
Drive Rivets:
Drive rivets, also called split rivets, have a flat, unheaded shaft with a scored or split end.
They are installed by driving a pin or nail into the split end to create a secure connection.
Peel Rivets:
Peel rivets are designed for applications with limited access to the backside of the assembly.
They feature a mandrel with a tapered end that expands the rivet body to create a tight joint.
Bulbing Rivets:
Bulbing rivets, also known as bulb-tite rivets, are designed for applications requiring a large bearing surface.
They have a bulbed end that spreads out upon installation, creating a secure connection.
Huck Bolts:
Huck bolts are high-strength fasteners that consist of a pin and collar.
They are installed by pulling the pin, which expands the collar and creates a permanent, vibration-resistant joint.
Orbital Rivets:
Orbital rivets are used in applications where a low-profile, flush finish is desired.
They create a strong and aesthetically pleasing joint without any protrusion on the surface.
The selection of the appropriate rivet type depends on factors such as accessibility, load-bearing requirements, installation method, desired appearance, and specific application needs. It is advisable to consult with riveting experts or design engineers to determine the most suitable rivet type for your metal sheet assembly.
Learn More About Metal Sheets Assembly Rivets
Rivets provide a reliable and durable fastening solution for metal sheet assembly, ensuring secure joints and structural integrity. The selection of the appropriate rivet type depends on factors such as the application requirements, joint strength needs, access to the assembly, material compatibility, and design considerations. Consulting with riveting experts or design engineers can help determine the most suitable rivet type for a specific metal sheet assembly project.
1.Composition:
Rivets are typically made of materials such as steel, aluminum, stainless steel, or copper.
The material choice depends on factors such as strength requirements, corrosion resistance, weight considerations, and compatibility with the joined metal sheets.
2.Basic Structure:
Rivets consist of a cylindrical shaft with a head on one end.
The opposite end of the shaft may be solid or include a mandrel (stem), depending on the type of rivet.
3.Installation Process:
Rivets are installed by inserting them into pre-drilled holes in the metal sheets.
The rivet is then deformed or expanded to secure the joint, creating a permanent connection.
4.Joint Strength:
Rivets provide high shear and tensile strength, making them suitable for applications requiring structural integrity.
The strength of the riveted joint depends on factors such as rivet diameter, material properties, hole size, and installation technique.
5.Applications:
Rivets are used in a wide range of industries, including automotive, aerospace, construction, metal fabrication, appliances, and electronics.
They are commonly employed in applications such as structural frames, panel assemblies, HVAC systems, furniture, and automotive bodywork.
6.Advantages:
Rivets offer several advantages for metal sheet assembly, including high strength, resistance to vibration, tamper resistance, and uniform load distribution.
They are also relatively inexpensive, require simple installation tools, and do not require access to both sides of the assembly in the case of blind rivets.
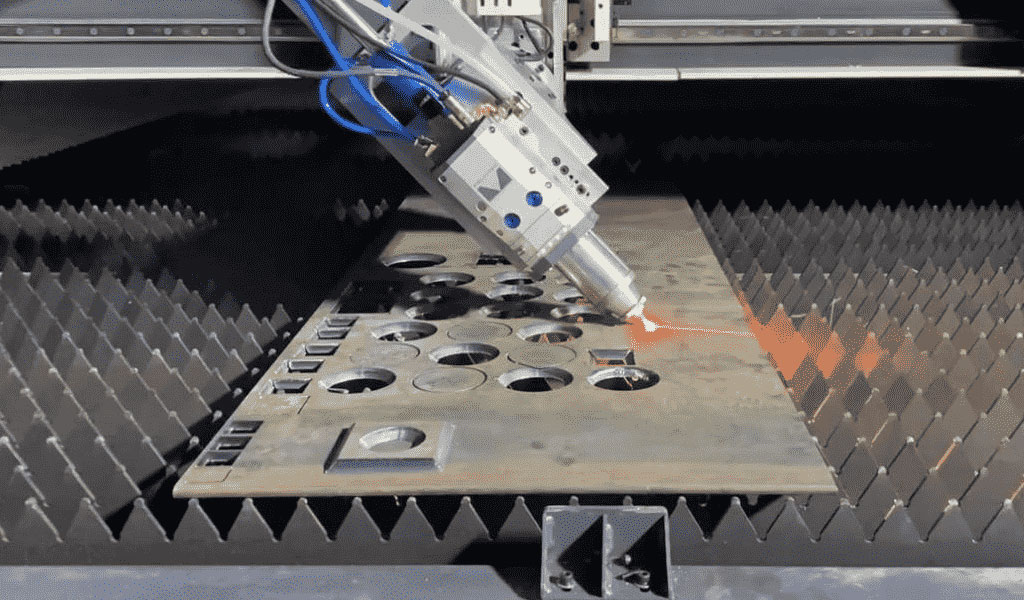
China Sheet Metal Fabrication Manufacturer
Custom precision metal fabrication services. Product specialties include UL® certified NEMA enclosures for various environmental conditions. Capabilities include punching, shearing, laser cutting, bending, machining, press brake forming, and welding. Materials worked with include mild steel, stainless steel, aluminum, brass, and more. Production volumes range from prototype to 10,000 pieces annually. Contract options include discrete orders, blanket orders, quarterly buys, and annual contracts. Value added services include inventory management, rapid prototyping, process development, design for manufacturability, inspection, supply chain management, transportation, and logistics. Industries served include aerospace, automotive, defense, electronic, electrical, entertainment, food and beverage, health, industrial automation, machinery, medical, oil, energy, power, sporting goods, telecommunications, transportation, and more.
using high quality materials
for your sheet metal parts orders
We uses a wide range of material selections for our sheet metal fabrication process. Among our materials are aluminum, stainless steel, brass, magnesium, copper, carbon steel, bronze, galvanized steel, and more. Each material is available in different grades and varieties. Rest assured that all the materials used for your sheet metal parts are durable, corrosion-resistant, long-lasting, rust-proof, wear-resistant, and high-performance. If you want a specific material to be used in the sheet metal fabrication process, don’t hesitate to contact us!
- Carbon Steel
- Stainless Steel
- Aluminum
- Brass
- Copper
- Magnesium
- Bronze
- Galvanized Steel
Why BE-CU is Trusted by 1000+ Clients
Our sheet metal fabrication covers a lot of benefits to many industries, businesses, or projects. Below are the advantages of our services.
- Affordable and Fast Production:We can quickly produce different sheet metal prototypes and final products. KDM offers speedy production while assuring high precision. Our high-volume production also allows us to have cost-effect sheet metal fabrication services.
- Excellent Strength to Weight Ratio:Through our advanced sheet metal fabrication, we can produce sheet metal parts that are lightweight yet durable. We assure high strength, scratch resistance, and corrosion resistance to all produced sheet metal products.
- Wide Range of Materials and Techniques Used:We are experts in different sheet metal fabrication techniques that allow us to produce complex parts with additional intricate features such as notches, slots, holes, etc. Our wide range of sheet metal materials can also withstand electrical, high heat, corrosion, and more.
Online Contact China Precision Sheet Metal Manufacturers
As a direct supplier of precision machined and finished complete components to all segments of the aerospace, semiconductor, automotive, and medical industries, including innovative high tech startups, BE-CU Sheet metal manufacturer is your trusted source for precision sheet metal fabrication services.
To learn more about our aluminum,stainless steel and other steel alloy sheet metal fabrication services, contact us, or give us a call at +86 153 8731 8440, and one of our expert associates will assist you. BE-CU is your trusted source for premium sheet metal fabrication services and metal spinning china manufacturer.