Aluminum C channels are essential components in a variety of construction and manufacturing applications. Their unique shape, strength, and lightweight properties make them a preferred choice for many industries. To harness the full potential of aluminum C channels, it is crucial to have a comprehensive understanding of their sizes and dimensions. In this article, we will delve into the world of aluminum C channel size charts, exploring their significance, and how they play a pivotal role in modern engineering and design.
Understanding Aluminum C Channels
Aluminum C channels are designed with a distinctive “C” shape, which allows them to provide structural support while minimizing weight. This versatility has made them a popular choice for a wide range of applications, including frame construction, mounting, and support systems. Aluminum C channels are not only strong but also corrosion-resistant, making them suitable for indoor and outdoor projects.
The Importance of a Size Chart
A well-structured aluminum C channel size chart is an invaluable resource for engineers, architects, and builders. It simplifies the selection process, ensuring that the right size is chosen for a specific project. Without a size chart, one might end up with channels that are either too large, wasting resources, or too small, compromising structural integrity. A size chart acts as a guide, eliminating guesswork and errors in the selection of C channels.
Key Parameters in a Size Chart
- Width (A): The width of the C channel, represented as “A” in the size chart, is a critical parameter. It determines the channel’s ability to provide support and distribute loads.
- Height (B): The height of the C channel, denoted as “B,” plays a significant role in its strength and stability. Taller channels are generally more robust.
- Thickness (T): The thickness of the aluminum C channel, represented as “T,” influences its rigidity and load-carrying capacity. Thicker channels can handle heavier loads.
- Web (C): The web, denoted as “C,” is the interior section of the C channel between the flanges. Its dimensions affect the overall structural performance of the channel.
Benefits of Using a Size Chart
- Accuracy: By referencing a size chart, you can accurately choose the right aluminum C channel for your project, minimizing the likelihood of costly mistakes.
- Efficiency: Size charts streamline the decision-making process, saving time during the planning and construction phases.
- Cost-Effectiveness: Selecting the correct size ensures that materials are used efficiently, reducing waste and cutting down on project costs.
- Safety: Properly sized channels guarantee the structural integrity of the project, enhancing safety for users and the longevity of the structure.
Applications of Aluminum C Channels
Aluminum C channels find applications in various industries:
- Construction: They are used for framing and support in buildings, bridges, and infrastructure projects.
- Manufacturing: In the manufacturing industry, C channels serve as structural components for conveyors, assembly lines, and machine frames.
- Transportation: Aluminum C channels are employed in the construction of lightweight trailers, reducing fuel consumption and increasing payload capacity.
- Renewable Energy: These channels are used in solar panel mounting systems due to their corrosion resistance and ease of installation.
Conclusion
Aluminum C channels are an indispensable part of modern construction and manufacturing. Their versatility, strength, and lightweight nature make them a preferred choice for engineers and architects. A well-structured aluminum C channel size chart is essential for ensuring that the right size is selected for each application, optimizing efficiency, cost-effectiveness, and safety. By understanding the significance of these size charts, we can unlock the full potential of aluminum C channels in a wide range of industries.
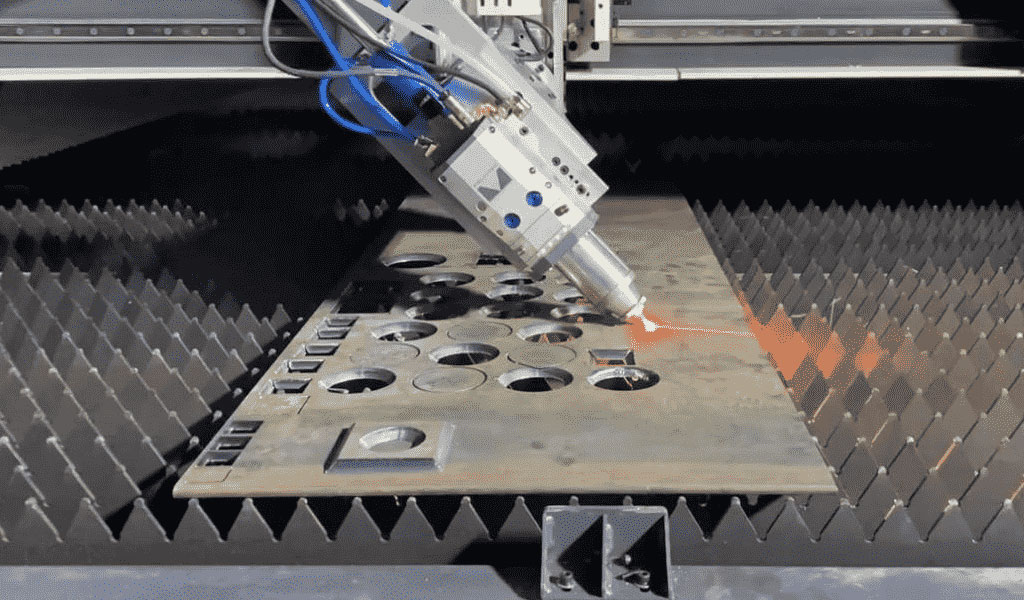
China Sheet Metal Fabrication Manufacturer
Custom precision metal fabrication services. Product specialties include UL® certified NEMA enclosures for various environmental conditions. Capabilities include punching, shearing, laser cutting, bending, machining, press brake forming, and welding. Materials worked with include mild steel, stainless steel, aluminum, brass, and more. Production volumes range from prototype to 10,000 pieces annually. Contract options include discrete orders, blanket orders, quarterly buys, and annual contracts. Value added services include inventory management, rapid prototyping, process development, design for manufacturability, inspection, supply chain management, transportation, and logistics. Industries served include aerospace, automotive, defense, electronic, electrical, entertainment, food and beverage, health, industrial automation, machinery, medical, oil, energy, power, sporting goods, telecommunications, transportation, and more.
using high quality materials
for your sheet metal parts orders
We uses a wide range of material selections for our sheet metal fabrication process. Among our materials are aluminum, stainless steel, brass, magnesium, copper, carbon steel, bronze, galvanized steel, and more. Each material is available in different grades and varieties. Rest assured that all the materials used for your sheet metal parts are durable, corrosion-resistant, long-lasting, rust-proof, wear-resistant, and high-performance. If you want a specific material to be used in the sheet metal fabrication process, don’t hesitate to contact us!
- Carbon Steel
- Stainless Steel
- Aluminum
- Brass
- Copper
- Magnesium
- Bronze
- Galvanized Steel
Why BE-CU is Trusted by 1000+ Clients
Our sheet metal fabrication covers a lot of benefits to many industries, businesses, or projects. Below are the advantages of our services.
- Affordable and Fast Production:We can quickly produce different sheet metal prototypes and final products. KDM offers speedy production while assuring high precision. Our high-volume production also allows us to have cost-effect sheet metal fabrication services.
- Excellent Strength to Weight Ratio:Through our advanced sheet metal fabrication, we can produce sheet metal parts that are lightweight yet durable. We assure high strength, scratch resistance, and corrosion resistance to all produced sheet metal products.
- Wide Range of Materials and Techniques Used:We are experts in different sheet metal fabrication techniques that allow us to produce complex parts with additional intricate features such as notches, slots, holes, etc. Our wide range of sheet metal materials can also withstand electrical, high heat, corrosion, and more.
Online Contact China Precision Sheet Metal Manufacturers
As a direct supplier of precision machined and finished complete components to all segments of the aerospace, semiconductor, automotive, and medical industries, including innovative high tech startups, BE-CU Sheet metal manufacturer is your trusted source for precision sheet metal fabrication services.
To learn more about our aluminum,stainless steel and other steel alloy sheet metal fabrication services, contact us, or give us a call at +86 153 8731 8440, and one of our expert associates will assist you. BE-CU is your trusted source for premium sheet metal fabrication services and metal spinning china manufacturer.