Junction boxes and pull boxes are two types of electrical enclosures used in electrical installations to house and protect electrical connections and wiring. While they serve similar purposes, there are some key differences between junction boxes and pull boxes.This article compares junction box vs pull box, including types, sizing and spacing between these electrical boxes.
The Definition Of Junction Box And Pull Box
Junction box and a pull box are both types of electrical enclosures used in electrical installations, but they serve slightly different purposes. Here are the definitions of each:
What Is Junction Box
Junction box is an electrical enclosure designed to house and protect electrical connections, splices, and terminations. It serves as a central point where electrical wires are joined together or branched off to different circuits. Junction boxes are essential for maintaining a safe and organized electrical system by containing and protecting the electrical connections from environmental elements, accidental contact, and potential hazards. Here’s a breakdown of the key features and functions of a junction box:
Enclosure:
A junction box is typically a small enclosure made of metal or plastic.
It provides a protective housing to prevent exposure of electrical connections, reducing the risk of accidental contact and damage.
Electrical Connections:
Inside the junction box, electrical wires are connected or spliced together using wire connectors, terminal blocks, or other suitable means.
The junction box facilitates the secure and insulated connection of wires, ensuring proper electrical continuity.
Cable Entry Points:
Junction boxes have multiple entry points, known as knockouts or conduit openings, where electrical cables or conduits can be inserted.
These entry points allow for the entry and exit of electrical wires, providing a means for cable routing and organization.
Protection and Safety:
The primary purpose of a junction box is to provide protection and safety for electrical connections.
It prevents wires from being exposed to moisture, dust, dirt, or other external factors that could potentially cause short circuits or electrical hazards.
Easy Access:
Junction boxes feature removable covers or lids, providing easy access to the interior for installation, maintenance, or troubleshooting purposes.
The covers are typically secured with screws or latches to ensure proper enclosure integrity.
Code Compliance:
Junction boxes must adhere to electrical codes and regulations that govern the size, material, installation, and usage of electrical enclosures.
Compliance with these standards ensures the safety, efficiency, and longevity of the electrical system.
Junction boxes are commonly used in residential, commercial, and industrial electrical installations. They are strategically placed along electrical circuits, typically at branching points or where splices are required. Proper installation and use of junction boxes promote electrical safety, facilitate organized wiring connections, and make future modifications or repairs more manageable.
What Is Pull Box
Pull box, also known as a junction and pull box, is an electrical enclosure used in electrical installations to provide an access point for pulling, splicing, and routing electrical cables or conductors. It is designed to accommodate the needs of cable management and facilitate the installation and maintenance of electrical wiring.Here are some key features and functions of a pull box:
Size and Design:
Pull boxes are typically larger in size compared to junction boxes and provide more interior space to accommodate multiple cables or conductors.
They are often rectangular in shape and constructed from metal or plastic materials.
Pull boxes feature removable covers or doors, allowing easy access to the interior for cable routing, splicing, or maintenance.
Cable Management and Routing:
Pull boxes are specifically designed to facilitate the pulling, organizing, and routing of electrical cables or conductors.
They provide ample space for managing multiple cables, ensuring they are properly supported and organized within the enclosure.
Cable Pulling:
Pull boxes have sufficient space to allow for the pulling of electrical cables during installation.
The spacious interior provides room for maneuvering and properly aligning the cables to ensure a smooth and safe pulling process.
Splicing and Connections:
Pull boxes accommodate the splicing and termination of electrical cables or conductors.
They provide a centralized location where multiple cables can be securely connected and spliced together using appropriate connectors or terminal blocks.
Accessibility:
Pull boxes feature removable covers or doors, allowing easy access for maintenance, troubleshooting, or modifications to the cables or connections.
This accessibility ensures that any necessary repairs, additions, or changes can be made efficiently.
Environmental Protection:
Pull boxes provide protection for the cables and electrical connections from environmental factors, such as moisture, dust, or accidental contact.
The enclosure helps maintain the integrity and safety of the electrical system.
Pull boxes are commonly used in commercial, industrial, and larger-scale electrical installations where there is a need for managing and organizing multiple cables. They serve as access points that enable efficient cable pulling, splicing, and routing, making installations and maintenance more manageable. Proper selection and installation of pull boxes are essential to ensure compliance with electrical codes and regulations and to maintain the safety and reliability of the electrical system.
While both junction boxes and pull boxes are used to house electrical connections, the main distinction lies in their primary functions. Junction boxes primarily serve as a central point for joining and branching electrical circuits, while pull boxes are specifically designed for facilitating the pulling, splicing, and routing of electrical cables or conductors. The choice between a junction box and a pull box depends on the specific requirements of the electrical installation, including the number of connections, the need for cable routing, and accessibility for maintenance or modifications.
The Types Of Junction Box And Pull Box
Junction boxes and pull boxes come in various types to accommodate different applications and requirements. Here are some common types of junction boxes and pull boxes:
Types of Junction Boxes:
Standard Junction Box:
This is the most common type of junction box used for general electrical connections and splices.
It is available in various shapes (rectangular, square, circular) and sizes to accommodate different wiring needs.
Standard junction boxes typically have multiple conduit entry points for cable entry and exit.
Weatherproof Junction Box:
Weatherproof junction boxes are designed to withstand outdoor environments and provide protection against moisture, dust, and other environmental elements.
They have sealed gaskets and covers to ensure a watertight and weather-resistant enclosure.
Explosion-Proof Junction Box:
Explosion-proof junction boxes are constructed with materials and designs that can contain and prevent the ignition of explosive gases or dust.
They are used in hazardous environments where there is a risk of flammable substances being present.
Terminal Junction Box:
Terminal junction boxes are specifically designed for terminating and connecting multiple electrical wires or conductors.
They often feature terminal blocks or connectors that simplify wiring connections.
Instrumentation Junction Box:
Instrumentation junction boxes are used in industrial settings to house electrical instrumentation equipment and provide a central point for instrument connections and signal routing.
Types of Pull Boxes:
Standard Pull Box:
Standard pull boxes are commonly used in electrical installations to facilitate cable pulling, splicing, and routing.
They provide ample space and access for cable management and are available in various sizes to accommodate different cable quantities.
Underground Pull Box:
Underground pull boxes are designed for burying underground and are constructed to withstand the pressure and environmental conditions associated with burial.
They often have additional features like watertight seals and corrosion-resistant materials.
Floor Pull Box:
Floor pull boxes are installed flush with the floor surface, providing an access point for cable routing in raised floor environments.
They are typically durable and can handle foot traffic or equipment loads.
Traffic Pull Box:
Traffic pull boxes are specifically designed for use in traffic signal and street lighting installations.
They are rugged, weather-resistant, and often feature secure covers to protect the electrical connections.
Handhole Pull Box:
Handhole pull boxes are used in utility applications for accessing and managing electrical connections and cables underground.
They are often installed at hand-reachable depths and feature covers that can be easily opened for maintenance or repairs.
It’s important to select the appropriate type of junction box or pull box based on the specific application requirements, environmental conditions, wiring needs, and compliance with electrical codes and regulations. Consulting with electrical professionals or following local guidelines can help ensure the proper selection and installation of the suitable type of junction box or pull box for your specific electrical project.
Junction Box Sizing Chart
You do not need to perform any calculations when sizing a junction box because it is standardized. Rather, look through the chat in NEC 314.16 to establish the minimum and maximum volume of your electrical junction box. The chat applies if the size of the conductors within the junction box range from 18 AWG all through to 6 AWG.Here’s a sample table chart illustrating the sizing of junction boxes based on the number and size of conductors:
Number of Conductors | Conductor Size (AWG) | Box Size (Cubic Inches) |
---|---|---|
1-2 | 14-10 | 12 |
3-4 | 14-10 | 18 |
5-6 | 14-10 | 21 |
7-8 | 14-10 | 24 |
9-10 | 14-10 | 30 |
11-12 | 14-10 | 36 |
13-14 | 14-10 | 42 |
15-16 | 14-10 | 50 |
17-18 | 14-10 | 58 |
19-20 | 14-10 | 68 |
Pull Box Sizing Chart
Sizing of pull box depends on the number and size of conductors, in addition to diameter and number of raceways.
For 4 AWG conductors and above, you should size the pull box in compliance with NEC 314.28. We will give a summary of the pull box sizing standards for common pull types, together with a calculation illustration.Here’s a sample table chart illustrating the sizing of pull boxes based on the number and size of conductors:
Number of Conductors | Conductor Size (AWG) | Box Size (Cubic Inches) |
---|---|---|
1-4 | 14-10 | 6×6 or 8×8 |
5-8 | 14-10 | 10×10 or 12×12 |
9-12 | 14-10 | 12×18 or 12×24 |
13-16 | 14-10 | 18×18 or 18×24 |
17-20 | 14-10 | 18×30 or 24×24 |
21-24 | 14-10 | 24×30 or 24×36 |
25-28 | 14-10 | 30×30 or 30×36 |
29-32 | 14-10 | 36×36 or 36×42 |
33-36 | 14-10 | 36×48 or 42×42 |
37-40 | 14-10 | 42×48 or 48×48 |
Online Sheet Metal Fabrication With Be-Cu
Junction boxes and pull boxes are important components of any electrical wiring connection. Contact us for quality electrical boxes and our staff will assist you throughout the process until you receive your products.
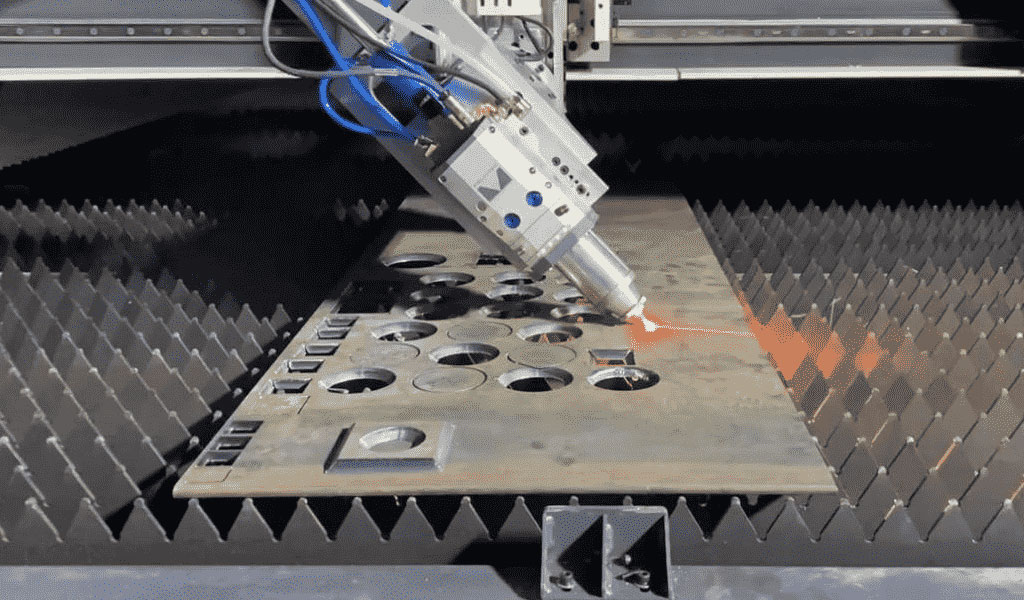
China Sheet Metal Fabrication Manufacturer
Custom precision metal fabrication services. Product specialties include UL® certified NEMA enclosures for various environmental conditions. Capabilities include punching, shearing, laser cutting, bending, machining, press brake forming, and welding. Materials worked with include mild steel, stainless steel, aluminum, brass, and more. Production volumes range from prototype to 10,000 pieces annually. Contract options include discrete orders, blanket orders, quarterly buys, and annual contracts. Value added services include inventory management, rapid prototyping, process development, design for manufacturability, inspection, supply chain management, transportation, and logistics. Industries served include aerospace, automotive, defense, electronic, electrical, entertainment, food and beverage, health, industrial automation, machinery, medical, oil, energy, power, sporting goods, telecommunications, transportation, and more.
using high quality materials
for your sheet metal parts orders
We uses a wide range of material selections for our sheet metal fabrication process. Among our materials are aluminum, stainless steel, brass, magnesium, copper, carbon steel, bronze, galvanized steel, and more. Each material is available in different grades and varieties. Rest assured that all the materials used for your sheet metal parts are durable, corrosion-resistant, long-lasting, rust-proof, wear-resistant, and high-performance. If you want a specific material to be used in the sheet metal fabrication process, don’t hesitate to contact us!
- Carbon Steel
- Stainless Steel
- Aluminum
- Brass
- Copper
- Magnesium
- Bronze
- Galvanized Steel
Why BE-CU is Trusted by 1000+ Clients
Our sheet metal fabrication covers a lot of benefits to many industries, businesses, or projects. Below are the advantages of our services.
- Affordable and Fast Production:We can quickly produce different sheet metal prototypes and final products. KDM offers speedy production while assuring high precision. Our high-volume production also allows us to have cost-effect sheet metal fabrication services.
- Excellent Strength to Weight Ratio:Through our advanced sheet metal fabrication, we can produce sheet metal parts that are lightweight yet durable. We assure high strength, scratch resistance, and corrosion resistance to all produced sheet metal products.
- Wide Range of Materials and Techniques Used:We are experts in different sheet metal fabrication techniques that allow us to produce complex parts with additional intricate features such as notches, slots, holes, etc. Our wide range of sheet metal materials can also withstand electrical, high heat, corrosion, and more.
Online Contact China Precision Sheet Metal Manufacturers
As a direct supplier of precision machined and finished complete components to all segments of the aerospace, semiconductor, automotive, and medical industries, including innovative high tech startups, BE-CU Sheet metal manufacturer is your trusted source for precision sheet metal fabrication services.
To learn more about our aluminum,stainless steel and other steel alloy sheet metal fabrication services, contact us, or give us a call at +86 153 8731 8440, and one of our expert associates will assist you. BE-CU is your trusted source for premium sheet metal fabrication services and metal spinning china manufacturer.