Compressed air is a versatile utility widely used in manufacturing processes across various industries. From powering pneumatic tools and conveying materials to ensuring product quality, compressed air plays a pivotal role. However, what often goes unnoticed is the importance of maintaining the quality and safety of compressed air. Compressed air testing is a critical aspect of manufacturing that ensures the reliability and efficiency of this vital resource. In this article, we will delve into the need for compressed air testing in manufacturing and its far-reaching implications on product quality, operational efficiency, and worker safety.
The Significance of Compressed Air
Compressed air serves as the fourth utility in manufacturing, following electricity, water, and gas. Its applications are diverse, including:
- Pneumatic Tools: Compressed air powers a multitude of tools and equipment, such as drills, grinders, and spray guns, allowing for precision and control in manufacturing processes.
- Conveyor Systems: Air-powered conveyor systems transport materials efficiently, reducing manual handling and enhancing productivity.
- Packaging: Compressed air is used in packaging machinery to seal, fill, and label products, ensuring their safety and quality.
- Cleanliness: Compressed air is employed for cleaning and purging, keeping machinery and products free from contaminants.
- HVAC Systems: Many manufacturing facilities rely on compressed air for controlling heating, ventilation, and air conditioning systems.
- Quality Control: In some industries, compressed air is a direct component of the product, like in food and beverage, where it’s used for bottling and packaging.
The Need for Compressed Air Testing
The quality and safety of compressed air are paramount, and ensuring these factors requires routine testing and maintenance. Here’s why compressed air testing is indispensable in manufacturing:
Product Quality Assurance
In industries like pharmaceuticals, food and beverage, and electronics, where compressed air directly contacts the product, any contamination can lead to severe quality issues. Compressed air testing helps identify and mitigate potential contaminants, ensuring that products meet stringent quality standards.
Energy Efficiency
Leaky compressed air systems can be a major source of energy waste. Testing helps pinpoint leaks, and by fixing these issues, manufacturers can significantly reduce energy consumption and operational costs.
Equipment Longevity
Contaminants and moisture in compressed air can damage equipment and machinery. Regular testing allows manufacturers to detect and address these issues early, prolonging the life of their assets and reducing maintenance expenses.
Safety and Compliance
In industries where compressed air is used for worker safety, like providing breathing air for confined space work, compliance with air quality standards is critical. Testing ensures that the air is safe for human use and complies with regulatory requirements.
Environmental Responsibility
Minimizing compressed air waste and preventing the release of contaminants into the environment aligns with sustainability goals. Compressed air testing supports these objectives by helping manufacturers reduce their environmental footprint.
The Testing Process
Compressed air testing involves sampling air from the system and analyzing it for various parameters, such as particle counts, moisture content, oil content, and microbiological contamination. The results are compared to industry-specific standards, which guide corrective actions and maintenance.
Conclusion
Compressed air is the unseen hero of manufacturing, powering a wide range of processes and equipment. However, its quality and safety are often overlooked. Compressed air testing is a critical component of manufacturing operations, ensuring product quality, energy efficiency, equipment longevity, safety, and environmental responsibility. By prioritizing the testing and maintenance of compressed air systems, manufacturers can unlock a world of benefits, from increased product quality to reduced operational costs, making it a wise investment for any manufacturing facility.
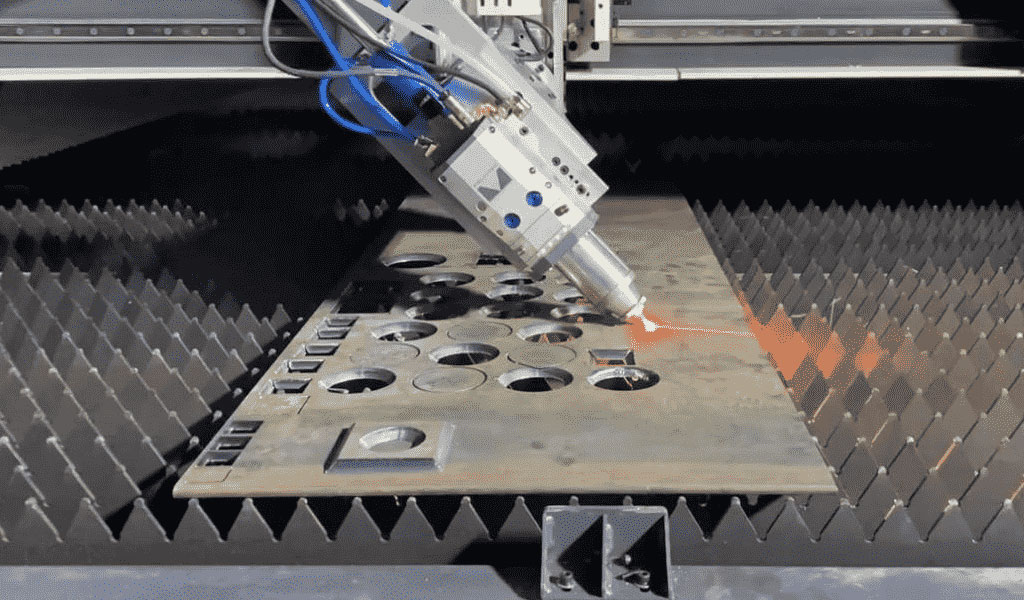
China Sheet Metal Fabrication Manufacturer
Custom precision metal fabrication services. Product specialties include UL® certified NEMA enclosures for various environmental conditions. Capabilities include punching, shearing, laser cutting, bending, machining, press brake forming, and welding. Materials worked with include mild steel, stainless steel, aluminum, brass, and more. Production volumes range from prototype to 10,000 pieces annually. Contract options include discrete orders, blanket orders, quarterly buys, and annual contracts. Value added services include inventory management, rapid prototyping, process development, design for manufacturability, inspection, supply chain management, transportation, and logistics. Industries served include aerospace, automotive, defense, electronic, electrical, entertainment, food and beverage, health, industrial automation, machinery, medical, oil, energy, power, sporting goods, telecommunications, transportation, and more.
using high quality materials
for your sheet metal parts orders
We uses a wide range of material selections for our sheet metal fabrication process. Among our materials are aluminum, stainless steel, brass, magnesium, copper, carbon steel, bronze, galvanized steel, and more. Each material is available in different grades and varieties. Rest assured that all the materials used for your sheet metal parts are durable, corrosion-resistant, long-lasting, rust-proof, wear-resistant, and high-performance. If you want a specific material to be used in the sheet metal fabrication process, don’t hesitate to contact us!
- Carbon Steel
- Stainless Steel
- Aluminum
- Brass
- Copper
- Magnesium
- Bronze
- Galvanized Steel
Why BE-CU is Trusted by 1000+ Clients
Our sheet metal fabrication covers a lot of benefits to many industries, businesses, or projects. Below are the advantages of our services.
- Affordable and Fast Production:We can quickly produce different sheet metal prototypes and final products. KDM offers speedy production while assuring high precision. Our high-volume production also allows us to have cost-effect sheet metal fabrication services.
- Excellent Strength to Weight Ratio:Through our advanced sheet metal fabrication, we can produce sheet metal parts that are lightweight yet durable. We assure high strength, scratch resistance, and corrosion resistance to all produced sheet metal products.
- Wide Range of Materials and Techniques Used:We are experts in different sheet metal fabrication techniques that allow us to produce complex parts with additional intricate features such as notches, slots, holes, etc. Our wide range of sheet metal materials can also withstand electrical, high heat, corrosion, and more.
Online Contact China Precision Sheet Metal Manufacturers
As a direct supplier of precision machined and finished complete components to all segments of the aerospace, semiconductor, automotive, and medical industries, including innovative high tech startups, BE-CU Sheet metal manufacturer is your trusted source for precision sheet metal fabrication services.
To learn more about our aluminum,stainless steel and other steel alloy sheet metal fabrication services, contact us, or give us a call at +86 153 8731 8440, and one of our expert associates will assist you. BE-CU is your trusted source for premium sheet metal fabrication services and metal spinning china manufacturer.