Sheet metal ductwork fabrication is a critical component of modern HVAC (Heating, Ventilation, and Air Conditioning) systems. These unassuming metal conduits play a pivotal role in maintaining indoor air quality, temperature control, and energy efficiency in homes, commercial buildings, and industrial facilities. While often hidden from view, they are the unsung heroes behind the comfort and health of countless individuals.
In this extensive guide, we will delve deep into the world of sheet metal ductwork fabrication, exploring its purpose, materials, design principles, manufacturing processes, installation techniques, maintenance, and the ever-evolving technologies shaping this industry. By the time you finish reading, you’ll have an in-depth understanding of what sheet metal ductwork is, why it matters, and how it’s fabricated to meet diverse HVAC requirements.
The Importance of Sheet Metal Ductwork
Sheet metal ductwork is a critical component of HVAC (Heating, Ventilation, and Air Conditioning) systems, and its importance cannot be overstated. In this section, we will explore the pivotal role that HVAC systems play in ensuring indoor comfort and air quality, why ductwork is crucial for the functioning of HVAC systems, and the significant impact of efficient ductwork on energy consumption.
The Role of HVAC Systems in Indoor Comfort and Air Quality
HVAC systems are the unsung heroes of modern indoor environments. Their primary purpose is to create and maintain a comfortable, safe, and healthy atmosphere within buildings. Here are some key aspects of their role:
- Temperature Control: HVAC systems are responsible for maintaining the desired temperature in both residential and commercial spaces. They ensure that occupants are neither too cold in the winter nor too hot in the summer.
- Ventilation: Proper ventilation is essential for indoor air quality. HVAC systems supply fresh outdoor air while expelling stale indoor air, preventing the buildup of pollutants, allergens, and odors.
- Humidity Regulation: HVAC systems can adjust humidity levels to maintain an ideal indoor environment. This is crucial for comfort, health, and the preservation of property.
- Air Filtration: High-quality air filters integrated into HVAC systems can remove particles, dust, pollen, and even microorganisms from the air, significantly improving indoor air quality.
- Energy Efficiency: Modern HVAC systems are designed to be energy-efficient, reducing the environmental impact and operating costs of buildings.
Why Ductwork Is Crucial for HVAC Systems
Ductwork is the circulatory system of an HVAC setup, responsible for distributing conditioned air to various parts of a building. Without ductwork, the entire HVAC system would be rendered ineffective. Here’s why ductwork is crucial:
- Air Distribution: Ducts carry conditioned air from the source (the HVAC unit) to the various rooms and spaces in a building. This distribution ensures that every area receives the intended level of heating, cooling, and ventilation.
- Zoning: Ductwork allows for zoning, meaning that different parts of a building can have independent temperature and humidity controls. This is especially important in larger buildings with diverse usage requirements.
- Airflow Control: Ductwork incorporates dampers and registers that enable precise control of airflow. This control is essential for maintaining uniform comfort and energy efficiency.
- Noise Control: Properly designed and installed ductwork helps minimize noise transmission from the HVAC system to occupied spaces. This is crucial for maintaining a peaceful indoor environment.
The Impact of Efficient Ductwork on Energy Consumption
Efficiency in ductwork design and fabrication has a significant impact on the energy consumption of HVAC systems. Inefficient duct systems can lead to substantial energy wastage. Here’s how efficient ductwork affects energy consumption:
- Reduced Energy Loss: Leaky ducts, inadequate insulation, and poorly designed ductwork can result in energy losses. Efficient duct systems minimize these losses, ensuring that the conditioned air reaches its destination without unnecessary waste.
- Balanced Airflow: Properly designed duct systems maintain balanced airflow throughout the building. This prevents overworking the HVAC system, which can lead to higher energy consumption.
- Zoning and Optimization: Zoned duct systems, combined with efficient controls, enable selective heating, cooling, and ventilation, reducing energy usage in unoccupied areas.
- Filter Efficiency: Well-maintained duct systems support the efficient operation of air filters, ensuring that they trap pollutants and allergens effectively without restricting airflow.
Sheet metal ductwork is a vital component of HVAC systems, which are central to maintaining indoor comfort and air quality. Efficient ductwork design and fabrication are critical for minimizing energy consumption and maximizing the performance of HVAC systems. In the following sections, we will delve deeper into the materials, design principles, fabrication processes, and installation techniques that make efficient ductwork possible.
Materials Used in Sheet Metal Ductwork
Sheet metal ductwork is constructed from a variety of materials, each chosen for its specific properties and suitability for different applications. In this section, we will explore the types of sheet metal commonly used in fabrication, the materials for insulation and lining, and the factors that influence material selection.
Types of Sheet Metal Used in Fabrication
- Galvanized Steel: Galvanized steel is one of the most popular materials for ductwork fabrication. It is known for its durability, corrosion resistance, and relatively low cost. Galvanized steel ducts are suitable for both residential and commercial applications.
- Aluminum: Aluminum ducts are lightweight, corrosion-resistant, and ideal for applications where weight reduction is a concern. They are often used in aerospace, automotive, and marine HVAC systems, as well as in residential and commercial settings.
- Stainless Steel: Stainless steel ducts are chosen for their exceptional resistance to corrosion and their ability to withstand extreme temperatures. They are commonly used in industrial and chemical environments and in applications where hygiene is critical, such as healthcare facilities and food processing plants.
- Copper: Copper ductwork is known for its excellent thermal conductivity. It is mainly used in specialized applications, such as in laboratories, high-end residential HVAC systems, and situations where heat transfer is a key factor.
- Fiberglass Reinforced Plastic (FRP): FRP ducts are non-metallic and resistant to corrosion, making them suitable for aggressive environments, including chemical processing plants and wastewater treatment facilities.
- PVC (Polyvinyl Chloride): PVC ducts are lightweight and resist chemical corrosion, making them ideal for certain industrial applications. They are commonly used in fume exhaust systems and corrosive chemical transport.
- Flexible Ducts: Flexible ducts are typically constructed with a metal wire coil surrounded by a plastic or foil covering. They are commonly used in residential HVAC systems due to their flexibility and ease of installation.
Insulation and Lining Materials
In addition to the sheet metal material used for the ductwork itself, insulation and lining materials are often applied to improve thermal and acoustic performance and to prevent condensation. Common insulation and lining materials include:
- Fiberglass Insulation: Fiberglass insulation is widely used for its thermal resistance properties. It is effective in conserving energy and maintaining desired temperature levels within the ducts.
- Polyurethane Foam: Polyurethane foam insulation provides excellent thermal insulation while also preventing condensation. It is commonly used in cold or hot HVAC systems.
- Neoprene and Rubber: These materials are used to provide sound insulation and vibration dampening in ductwork, reducing noise transmission and improving occupant comfort.
- Aluminum Foil: Aluminum foil is often used as a lining material for ducts, as it helps to control condensation and air leakage.
Factors Influencing Material Selection
The choice of materials for sheet metal ductwork fabrication is influenced by a variety of factors, including:
- Environmental Conditions: The environment in which the ductwork will be installed plays a significant role. For instance, corrosive atmospheres may require stainless steel or PVC ducts, while standard residential applications may use galvanized steel or aluminum.
- Temperature Requirements: Ducts in high-temperature applications require materials with excellent heat resistance, such as stainless steel or special high-temperature insulation.
- Budget Constraints: Cost considerations often dictate material choices. While some materials may be more durable or offer superior performance, they can also be more expensive.
- Aesthetics: In some cases, the appearance of the ductwork is a factor. Copper or stainless steel, for instance, may be chosen for their aesthetic appeal in high-end residential or commercial installations.
- Regulatory Compliance: Building codes and safety regulations may specify the materials that can be used in certain applications. Compliance is essential to meet safety and environmental standards.
- Energy Efficiency: For energy-efficient HVAC systems, materials that minimize heat transfer and condensation are preferred.
- Maintenance Requirements: The ease of maintenance and cleaning is a consideration, as some materials may require more frequent cleaning or have specific cleaning requirements.
The choice of materials in sheet metal ductwork fabrication is a critical decision that impacts the performance, durability, and cost-effectiveness of HVAC systems. It is essential to consider the specific requirements of each project and select materials that align with those needs to ensure optimal functionality and longevity.
Ductwork Design Principles
Ductwork design is a crucial element of HVAC systems, and it directly impacts the efficiency, comfort, and effectiveness of the system. In this section, we will explore the key design principles, including sizing and layout considerations, airflow dynamics and pressure balancing, and the importance of acoustic and thermal insulation requirements.
Sizing and Layout Considerations
- Sizing Ducts: The sizing of ducts is a fundamental aspect of design. Ducts should be appropriately sized to ensure that they can deliver the required airflow without excessive pressure drops. Undersized ducts can lead to reduced system performance, while oversized ducts may result in inefficiency and increased costs.
- Balancing Airflow: A well-designed ductwork system maintains balanced airflow throughout the building. This means that each room or zone receives the right amount of conditioned air. Balancing dampers and registers are used to achieve this balance.
- Zoning: Zoning is the practice of dividing a building into different zones, each with its own thermostat and independent control of the HVAC system. Proper zoning allows for energy-efficient temperature control, as only occupied areas are conditioned, while unoccupied areas are not.
- Layout and Routing: The layout and routing of ducts should be carefully planned to minimize obstructions, maintain accessibility for future maintenance, and ensure even air distribution. Ducts may be installed in attics, basements, or concealed within walls and ceilings.
Airflow Dynamics and Pressure Balancing
- Airflow Dynamics: Understanding the principles of airflow dynamics is crucial for efficient ductwork design. Air moves from high-pressure areas to low-pressure areas, and ducts are designed to facilitate this movement while minimizing turbulence. Smooth, well-designed transitions and curves in the ducts help maintain airflow efficiency.
- Pressure Balancing: Pressure balancing ensures that air is distributed evenly throughout the system. Balancing dampers and diffusers are used to achieve this balance. When the pressure in one part of the ductwork system is higher than in another, it can result in uneven airflow and decreased comfort.
- Return Air Path: Properly designed return air pathways are essential. Return air ducts should be positioned strategically to extract air from the occupied spaces efficiently, ensuring that the air is recirculated through the HVAC system and conditioned before redistribution.
Acoustic and Thermal Insulation Requirements
- Acoustic Insulation: Acoustic comfort is a critical consideration in HVAC design. Ductwork can transmit noise from the HVAC unit to occupied spaces. Acoustic insulation materials, such as fiberglass or foam, are used to reduce sound transmission. Duct liners and acoustic baffles can also be employed to absorb sound and minimize noise pollution.
- Thermal Insulation: In applications where temperature control is crucial, such as in heating or cooling ducts, thermal insulation is essential. Insulating ducts prevents heat loss or gain, ensuring that the conditioned air remains at the desired temperature as it travels through the system. This insulation is particularly important in extreme climates.
- Condensation Prevention: Insulation also helps prevent condensation on duct surfaces. When warm, moist air comes into contact with cooler ductwork, condensation can occur. Insulation with a vapor barrier prevents this, avoiding damage to the ducts and surrounding structures.
- Energy Efficiency: Proper insulation enhances energy efficiency. It reduces heat exchange with the surrounding environment, resulting in less energy consumption to maintain desired indoor temperatures.
Ductwork design principles are essential for the optimal functioning of HVAC systems. Sizing and layout considerations, airflow dynamics, and pressure balancing ensure that conditioned air reaches its destination efficiently and evenly. Additionally, the use of acoustic and thermal insulation materials is crucial to maintain acoustic comfort and energy efficiency while preventing condensation in the ducts. A well-designed ductwork system is the backbone of an effective HVAC system, delivering comfort, energy savings, and indoor air quality.
Fabrication Processes
Fabricating sheet metal ductwork involves a series of processes that transform raw materials into functional ducts. In this section, we’ll explore the choice between traditional handcrafting and modern automation, cutting, bending, and forming techniques, as well as welding, sealing, and finishing methods.
Traditional Handcrafting vs. Modern Automation
- Traditional Handcrafting: Historically, sheet metal ductwork was created through manual processes, involving skilled craftsmen who cut, bent, and formed the metal by hand. While this approach allowed for customization and attention to detail, it was time-consuming and had limitations in terms of precision and consistency.
- Modern Automation: In recent years, automation has become increasingly prevalent in ductwork fabrication. Computer Numerical Control (CNC) machines, laser cutting, and automated roll formers are now widely used. These machines offer advantages such as speed, precision, and the ability to produce large quantities of ducts with consistent quality.
Cutting, Bending, and Forming Techniques
- Cutting: Cutting is the first step in ductwork fabrication. Various methods are employed, including shearing, plasma cutting, or laser cutting. These methods produce clean, precise cuts in the sheet metal. The choice of cutting method depends on the material and the specific design requirements.
- Bending: Ducts often require precise bending to achieve the desired shape. This is typically done using press brakes or roll formers. Bending machines are programmed to bend the metal accurately, ensuring that it conforms to the required duct shape.
- Forming: The process of forming involves shaping the ductwork components. It can include processes such as beading (creating raised ridges for reinforcement), flanging (forming an edge for easy connection), and grooving (making seams or joints). Forming is essential for ensuring structural integrity and airtight connections.
Welding, Sealing, and Finishing Methods
- Welding: In some cases, ductwork components are joined together using welding techniques. This can provide a strong, permanent connection, but it’s not always necessary. Welding methods may include MIG (Metal Inert Gas) or TIG (Tungsten Inert Gas) welding. The choice of welding method depends on the material and application.
- Sealing: Achieving airtight duct connections is crucial to prevent air leakage. Sealing methods include using gaskets, mastic sealants, and specially designed duct connectors. Sealing ensures that conditioned air is delivered efficiently without loss.
- Finishing: Finishing involves preparing the ducts for installation. This can include cleaning, deburring, and painting or coating to protect the metal from corrosion and to provide a professional appearance. Finishing also helps to ensure that the ductwork is free from contaminants before installation.
- Insulation: In some applications, insulation is added to the exterior of the ducts to prevent condensation and maintain temperature control. Insulation materials are wrapped around the ducts and secured in place with adhesives or mechanical fasteners.
The fabrication of sheet metal ductwork involves a range of processes, including cutting, bending, and forming, as well as the choice between traditional handcrafting and modern automation. Welding, sealing, and finishing methods are essential to ensure the ducts are structurally sound, airtight, and ready for installation. The choice of fabrication techniques and methods depends on factors like material, project requirements, and the desired level of automation and precision.
Installation of Sheet Metal Ductwork
Proper installation of sheet metal ductwork is essential to ensure that the HVAC system operates efficiently and effectively. In this section, we will explore the best practices for on-site assembly, the use of support systems and hangers, and the critical process of connecting ductwork to HVAC components.
Best Practices for On-Site Assembly
- Plan and Layout: Before starting the installation, careful planning and layout are essential. Ensure that the ductwork routes and connections are well thought out, and any potential obstacles or obstructions are identified in advance.
- Measure Twice, Cut Once: The old adage holds true in ductwork installation. Accurate measurements are critical to ensure that ducts are cut to the correct length and that they fit precisely in the designated locations.
- Seam and Joint Connections: When assembling duct sections, ensure that seams and joints are properly aligned and sealed. This prevents air leakage and maintains the efficiency of the HVAC system. Use the appropriate sealing materials and methods.
- Secure Duct Sections: Duct sections should be securely fastened to one another. Proper connectors, fasteners, and brackets should be used to maintain structural integrity and airtight connections.
- Alignment and Leveling: Ducts should be installed in a way that ensures they are level and correctly aligned. This not only looks more professional but also aids in the efficiency of the system.
Support Systems and Hangers
- Hangers and Supports: Ducts need to be properly supported to prevent sagging and maintain structural integrity. Hangers and supports should be used at regular intervals to hold the weight of the ducts.
- Vibration Isolation: In some cases, ducts may require vibration isolation to prevent noise and structural damage. Vibration isolators can be added to hangers to absorb vibrations.
- Thermal Expansion: Ducts may expand and contract with changes in temperature. Expansion joints or flexible connectors can be used to accommodate these movements and prevent stress on the ductwork.
Connection to HVAC Components
- Transition Connections: The connection of ductwork to HVAC components like air handlers, furnaces, or vents should be carefully designed and executed. Transition pieces are often used to connect ducts of different sizes and shapes to the HVAC equipment.
- Sealing and Insulation: Proper sealing is crucial at these connection points to prevent air leakage. Use gaskets, sealants, and insulation as necessary to ensure airtight connections and prevent condensation.
- Balancing Dampers: Balancing dampers should be installed at strategic locations to regulate airflow. They allow for fine-tuning of the system to ensure that conditioned air is distributed evenly throughout the building.
- Air Filters: Ensure that air filters are easily accessible and properly installed. Air filters are essential for maintaining indoor air quality and protecting the HVAC system from contaminants.
- Final Inspection: After installation, a thorough inspection should be conducted to verify that all ducts are securely fastened, insulated, and sealed correctly. This step ensures that the system operates efficiently and meets safety and code requirements.
- System Testing: Conduct system testing, including airflow measurements and pressure testing, to verify that the HVAC system is functioning as intended. Any issues or deficiencies should be addressed before the system is put into operation.
The installation of sheet metal ductwork involves careful planning, precise assembly, proper support systems, and secure connections to HVAC components. Following best practices during installation is essential to ensure the efficiency and effectiveness of the HVAC system, as well as to maintain indoor air quality and occupant comfort.
Technological Advances in Sheet Metal Ductwork Fabrication
The field of sheet metal ductwork fabrication has undergone significant technological advancements that have revolutionized the industry. In this section, we will explore these technological advances, including the introduction of digital design and modeling, the role of Computer Numerical Control (CNC) machines, and the emergence of smart ductwork solutions and automation.
Introduction to Digital Design and Modeling
- Digital Design Software: The adoption of digital design software has transformed the way ductwork is conceptualized and created. CAD (Computer-Aided Design) and BIM (Building Information Modeling) software enable designers to create precise 3D models of ductwork systems. This digital representation allows for better visualization and planning.
- Design Optimization: Digital design tools help optimize ductwork systems for efficiency and cost-effectiveness. Engineers can simulate airflow, heat transfer, and pressure dynamics, ensuring that the system meets performance requirements.
- Collaboration and Coordination: Digital design tools facilitate collaboration among various stakeholders, including architects, engineers, and contractors. This ensures that the ductwork is seamlessly integrated into the overall building design.
Role of Computer Numerical Control (CNC) Machines
- Precision Fabrication: CNC machines, such as laser cutters, plasma cutters, and press brakes, have revolutionized sheet metal fabrication. These machines are capable of cutting, bending, and forming metal with exceptional precision, reducing human error and material waste.
- Speed and Efficiency: CNC machines are highly efficient and can produce ductwork components quickly. This leads to shorter lead times and faster project completion.
- Complex Shapes: CNC machines can create intricate and complex ductwork shapes that would be challenging to achieve through traditional handcrafting. This flexibility allows for innovative and custom designs.
Smart Ductwork Solutions and Automation
- Automated Assembly: Automation has extended beyond fabrication to ductwork assembly. Automated systems can piece together duct sections, apply seals, and install fasteners with high precision. This streamlines the installation process and reduces labor costs.
- Sensors and Monitoring: Smart ductwork solutions are equipped with sensors that monitor temperature, humidity, and air quality. These sensors can transmit data to building management systems, enabling real-time adjustments and energy optimization.
- Variable Air Volume (VAV) Systems: VAV systems are becoming increasingly popular. These systems automatically adjust airflow rates based on building occupancy and load. This reduces energy consumption and improves indoor air quality.
- Remote Control and Optimization: Smart ductwork systems can be controlled remotely, allowing for adjustments and troubleshooting without on-site presence. Building managers can optimize HVAC systems and respond to issues promptly.
- Energy Efficiency: Automation and smart technologies help reduce energy consumption by optimizing airflow, temperature, and other parameters. This leads to lower operating costs and reduced environmental impact.
Technological advances in sheet metal ductwork fabrication have significantly improved the design, production, and functionality of ductwork systems. Digital design and modeling tools enhance planning and coordination, CNC machines offer precision and speed in fabrication, and smart ductwork solutions and automation provide efficient, energy-saving, and remotely controlled HVAC systems. These advances have revolutionized the industry, providing more efficient, cost-effective, and environmentally friendly solutions for indoor climate control.
The Future of Sheet Metal Ductwork
The field of sheet metal ductwork fabrication is evolving rapidly, driven by technological advancements, changing industry needs, and environmental considerations. In this section, we’ll explore emerging trends in HVAC and ductwork and potential innovations that are poised to impact the industry.
Emerging Trends in HVAC and Ductwork
- Energy Efficiency: Energy efficiency remains a top priority in HVAC and ductwork design. Emerging trends focus on reducing energy consumption through improved insulation materials, advanced sealing techniques, and the use of energy-efficient HVAC components. This not only benefits the environment but also reduces operational costs for building owners.
- Indoor Air Quality (IAQ): The importance of indoor air quality has gained considerable attention, especially in the wake of health and wellness concerns. Ductwork design is evolving to accommodate better air filtration, humidity control, and advanced ventilation systems that enhance IAQ.
- Sustainability: Sustainable practices are increasingly integrated into ductwork fabrication. This includes the use of environmentally friendly materials, recycling of old ductwork, and the development of ductwork systems that minimize resource consumption and waste.
- Digitization and Automation: The integration of digital technology and automation in HVAC systems is expected to continue to grow. Smart ductwork solutions, combined with advanced sensors and IoT (Internet of Things) connectivity, will enable better control, monitoring, and maintenance of ductwork systems.
- Prefabrication: Prefabrication and modular ductwork components are becoming more popular. These approaches allow for quicker installation, reduced labor costs, and enhanced precision in manufacturing.
- Customization: The demand for customized ductwork systems is on the rise. Advances in digital design and CNC fabrication allow for ductwork to be tailor-made to fit specific building and HVAC system requirements.
Potential Innovations and Their Impact on the Industry
- Nanotechnology: The use of nanomaterials for coatings and insulation in ductwork could lead to superior thermal properties and reduced energy loss. Nanotechnology may also provide self-cleaning and antimicrobial properties, improving IAQ.
- 3D Printing: 3D printing of ductwork components may become more common, allowing for intricate designs and reduced waste. This technology can be especially useful for custom and one-off projects.
- Sustainable Materials: Innovations in sustainable materials, such as bio-based composites and recyclable metal alloys, can reduce the environmental footprint of ductwork fabrication. These materials may become more prevalent in the industry.
- AI and Machine Learning: AI and machine learning applications may enhance predictive maintenance and system optimization. AI algorithms can detect potential issues in ductwork systems and recommend solutions before they become major problems.
- Aerogels: Aerogels, highly porous materials with excellent insulating properties, may find applications in ductwork insulation, reducing heat transfer and improving energy efficiency.
- Ductless HVAC: The growth of ductless HVAC systems may reduce the need for extensive ductwork, especially in residential settings. Ductless systems are more efficient and flexible, providing a compelling alternative to traditional ductwork.
- Hybrid HVAC Systems: The development of hybrid HVAC systems that combine traditional ductwork with newer technologies like ductless systems and radiant heating/cooling may provide more versatile and energy-efficient solutions.
The future of sheet metal ductwork is bright, with a focus on sustainability, energy efficiency, and advanced technologies. As innovations continue to shape the industry, ductwork systems will play a pivotal role in creating healthier, more comfortable, and environmentally responsible indoor environments.
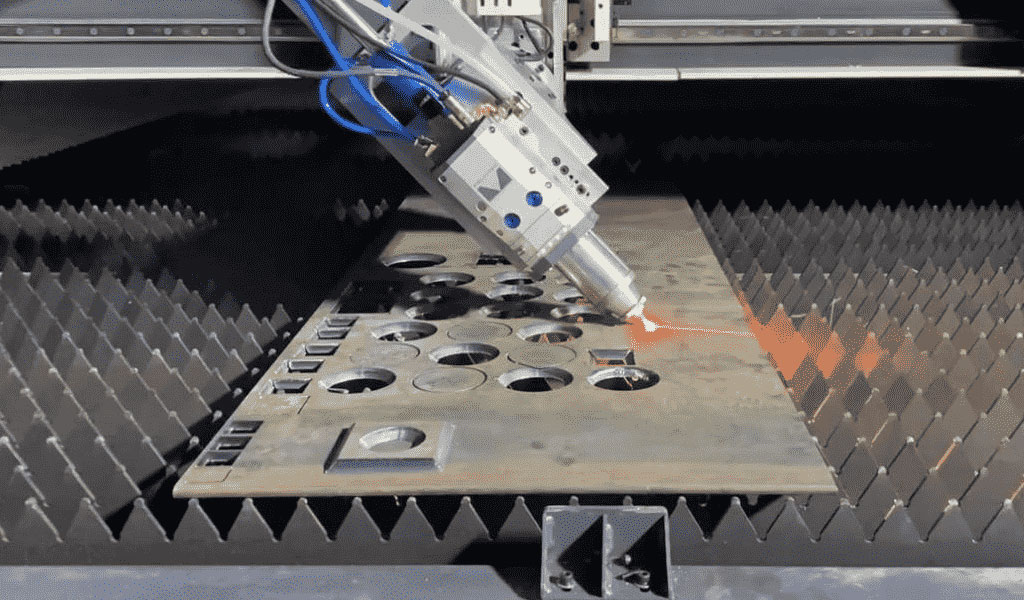
China Sheet Metal Fabrication Manufacturer
Custom precision metal fabrication services. Product specialties include UL® certified NEMA enclosures for various environmental conditions. Capabilities include punching, shearing, laser cutting, bending, machining, press brake forming, and welding. Materials worked with include mild steel, stainless steel, aluminum, brass, and more. Production volumes range from prototype to 10,000 pieces annually. Contract options include discrete orders, blanket orders, quarterly buys, and annual contracts. Value added services include inventory management, rapid prototyping, process development, design for manufacturability, inspection, supply chain management, transportation, and logistics. Industries served include aerospace, automotive, defense, electronic, electrical, entertainment, food and beverage, health, industrial automation, machinery, medical, oil, energy, power, sporting goods, telecommunications, transportation, and more.
using high quality materials
for your sheet metal parts orders
We uses a wide range of material selections for our sheet metal fabrication process. Among our materials are aluminum, stainless steel, brass, magnesium, copper, carbon steel, bronze, galvanized steel, and more. Each material is available in different grades and varieties. Rest assured that all the materials used for your sheet metal parts are durable, corrosion-resistant, long-lasting, rust-proof, wear-resistant, and high-performance. If you want a specific material to be used in the sheet metal fabrication process, don’t hesitate to contact us!
- Carbon Steel
- Stainless Steel
- Aluminum
- Brass
- Copper
- Magnesium
- Bronze
- Galvanized Steel
Why BE-CU is Trusted by 1000+ Clients
Our sheet metal fabrication covers a lot of benefits to many industries, businesses, or projects. Below are the advantages of our services.
- Affordable and Fast Production:We can quickly produce different sheet metal prototypes and final products. KDM offers speedy production while assuring high precision. Our high-volume production also allows us to have cost-effect sheet metal fabrication services.
- Excellent Strength to Weight Ratio:Through our advanced sheet metal fabrication, we can produce sheet metal parts that are lightweight yet durable. We assure high strength, scratch resistance, and corrosion resistance to all produced sheet metal products.
- Wide Range of Materials and Techniques Used:We are experts in different sheet metal fabrication techniques that allow us to produce complex parts with additional intricate features such as notches, slots, holes, etc. Our wide range of sheet metal materials can also withstand electrical, high heat, corrosion, and more.
Online Contact China Precision Sheet Metal Manufacturers
As a direct supplier of precision machined and finished complete components to all segments of the aerospace, semiconductor, automotive, and medical industries, including innovative high tech startups, BE-CU Sheet metal manufacturer is your trusted source for precision sheet metal fabrication services.
To learn more about our aluminum,stainless steel and other steel alloy sheet metal fabrication services, contact us, or give us a call at +86 153 8731 8440, and one of our expert associates will assist you. BE-CU is your trusted source for premium sheet metal fabrication services and metal spinning china manufacturer.