In the world of metal fabrication, welding is a fundamental process that demands precision, consistency, and efficiency. With the advancements in technology, welding automation has become a game-changer for fabrication shops, promising increased productivity and higher quality welds. However, making the transition to welding automation is not as simple as purchasing robotic equipment. There are essential steps to be taken to prepare your fab shop for this transformation. In this article, we will explore the three crucial steps to get your fab shop ready for welding automation.
Step 1: Assess Your Current Operations
Before diving into welding automation, it is crucial to assess your current welding operations thoroughly. This step involves evaluating the existing welding processes, equipment, and workforce capabilities. By conducting a comprehensive analysis, you can identify the areas in which automation can be most beneficial.
1.1 Review Existing Welding Processes
Begin by reviewing the various welding processes your fab shop utilizes, such as MIG, TIG, or stick welding. Understand the specific applications and challenges associated with each process. This analysis will help determine which processes are most suitable for automation.
1.2 Equipment Evaluation
Examine the condition and performance of your current welding equipment. Ensure that your machines are well-maintained and in optimal working condition. Consider upgrading or replacing outdated equipment to align with the requirements of automation systems.
1.3 Workforce Skill Assessment
Evaluate the skill set of your welding workforce. Identify the strengths and weaknesses of your welders, and provide training as needed to prepare them for working alongside automated systems or programming and maintaining robotic welding machines.
Step 2: Define Your Automation Goals and Objectives
Once you have a clear understanding of your existing operations, it’s time to define your goals and objectives for welding automation. What do you want to achieve by implementing automated welding systems? Common goals include:
2.1 Increased Productivity
Automation can significantly boost productivity by reducing cycle times and eliminating the need for breaks. Determine the level of productivity improvement you aim to achieve.
2.2 Improved Quality and Consistency
Welding automation provides precise control, resulting in consistently high-quality welds. Establish the quality standards you want to meet or exceed.
2.3 Cost Reduction
Automation can reduce labor costs and minimize the need for rework. Calculate the potential cost savings and return on investment (ROI) that automation can deliver.
2.4 Enhanced Safety
Consider how automation can enhance workplace safety by reducing exposure to hazardous welding environments and fumes. Prioritize safety in your objectives.
2.5 Increased Competitiveness
Automation can give your fab shop a competitive edge in the market. Determine how automation can help you win more business and stay ahead of the competition.
Step 3: Select the Right Welding Automation Equipment
Choosing the right welding automation equipment is a critical decision that will significantly impact the success of your transition. Consider the following factors when making your selection:
3.1 Automation Type
Determine the type of automation that best suits your operations. Options include robotic welding arms, welding positioners, and welding manipulators. Select the one that aligns with your specific welding processes and goals.
3.2 Integration with Existing Systems
Ensure that the chosen automation equipment can seamlessly integrate with your existing infrastructure, including welding power sources, safety systems, and control software.
3.3 Training and Support
Select equipment from manufacturers who offer comprehensive training and support. Proper training is vital for your workforce to operate and maintain the automation system effectively.
3.4 Scalability
Consider your future growth and the potential need for additional automation systems. Choose equipment that is scalable to accommodate your evolving needs.
Conclusion
Preparing your fab shop for welding automation is a strategic decision that can revolutionize your metal fabrication operations. By systematically assessing your current state, defining clear objectives, and selecting the right equipment, you can embark on this transformative journey with confidence. Welding automation holds the promise of increased productivity, improved quality, cost savings, enhanced safety, and a competitive advantage in the market. It’s time to embrace the future of fabrication and unlock the full potential of your fab shop through automation.
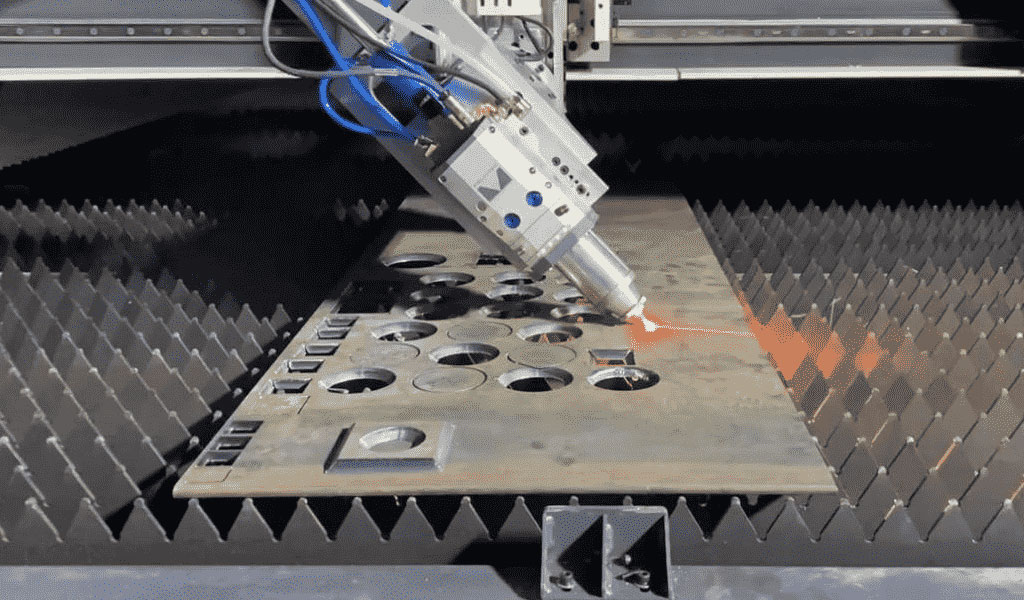
China Sheet Metal Fabrication Manufacturer
Custom precision metal fabrication services. Product specialties include UL® certified NEMA enclosures for various environmental conditions. Capabilities include punching, shearing, laser cutting, bending, machining, press brake forming, and welding. Materials worked with include mild steel, stainless steel, aluminum, brass, and more. Production volumes range from prototype to 10,000 pieces annually. Contract options include discrete orders, blanket orders, quarterly buys, and annual contracts. Value added services include inventory management, rapid prototyping, process development, design for manufacturability, inspection, supply chain management, transportation, and logistics. Industries served include aerospace, automotive, defense, electronic, electrical, entertainment, food and beverage, health, industrial automation, machinery, medical, oil, energy, power, sporting goods, telecommunications, transportation, and more.
using high quality materials
for your sheet metal parts orders
We uses a wide range of material selections for our sheet metal fabrication process. Among our materials are aluminum, stainless steel, brass, magnesium, copper, carbon steel, bronze, galvanized steel, and more. Each material is available in different grades and varieties. Rest assured that all the materials used for your sheet metal parts are durable, corrosion-resistant, long-lasting, rust-proof, wear-resistant, and high-performance. If you want a specific material to be used in the sheet metal fabrication process, don’t hesitate to contact us!
- Carbon Steel
- Stainless Steel
- Aluminum
- Brass
- Copper
- Magnesium
- Bronze
- Galvanized Steel
Why BE-CU is Trusted by 1000+ Clients
Our sheet metal fabrication covers a lot of benefits to many industries, businesses, or projects. Below are the advantages of our services.
- Affordable and Fast Production:We can quickly produce different sheet metal prototypes and final products. KDM offers speedy production while assuring high precision. Our high-volume production also allows us to have cost-effect sheet metal fabrication services.
- Excellent Strength to Weight Ratio:Through our advanced sheet metal fabrication, we can produce sheet metal parts that are lightweight yet durable. We assure high strength, scratch resistance, and corrosion resistance to all produced sheet metal products.
- Wide Range of Materials and Techniques Used:We are experts in different sheet metal fabrication techniques that allow us to produce complex parts with additional intricate features such as notches, slots, holes, etc. Our wide range of sheet metal materials can also withstand electrical, high heat, corrosion, and more.
Online Contact China Precision Sheet Metal Manufacturers
As a direct supplier of precision machined and finished complete components to all segments of the aerospace, semiconductor, automotive, and medical industries, including innovative high tech startups, BE-CU Sheet metal manufacturer is your trusted source for precision sheet metal fabrication services.
To learn more about our aluminum,stainless steel and other steel alloy sheet metal fabrication services, contact us, or give us a call at +86 153 8731 8440, and one of our expert associates will assist you. BE-CU is your trusted source for premium sheet metal fabrication services and metal spinning china manufacturer.