Welding is a fundamental process in various industries, from manufacturing to construction. However, it generates harmful fumes and particulate matter that can pose significant health risks to workers. To mitigate these dangers, localized weld fume control systems play a crucial role. In this article, we’ll explore six design considerations for achieving effective localized weld fume control, ensuring a safer and healthier work environment.
Understanding the Fume Generation
Effective localized weld fume control begins with a comprehensive understanding of the fume generation process. Various welding methods, materials, and workpiece geometries can influence the type and volume of fumes produced. Therefore, designers must consider these variables to tailor the control system accordingly. Factors such as the welding process, welding materials, and operator habits should be carefully analyzed.
Proper Hood Design
The heart of any localized weld fume control system is the hood. A well-designed hood should capture fumes at the source, preventing them from spreading into the workspace. Consider the type of welding, positioning of the hood, and the shape and size of the workpiece. A poorly designed hood can compromise fume capture efficiency and, ultimately, worker safety.
Adequate Airflow and Ventilation
Ensuring proper airflow and ventilation is crucial for effective weld fume control. Designers must calculate the required airflow rates to maintain a clean and safe working environment. Adequate ventilation also helps maintain a negative pressure gradient, preventing fumes from escaping into the surrounding area.
Filtration and Treatment Systems
After capturing the fumes, they need to be treated and filtered to remove hazardous particulates and gases. The choice of filtration and treatment methods depends on the specific contaminants produced during welding. Designers should consider options like mechanical filtration, electrostatic precipitation, and activated carbon adsorption systems. The goal is to achieve the highest level of air quality while minimizing maintenance requirements.
System Flexibility
Welding operations often involve a variety of workpieces and configurations. Therefore, a localized weld fume control system should be designed with flexibility in mind. This means adjustable hoods, ducting, and capture arms to accommodate various welding scenarios. A flexible system can adapt to different work environments, ensuring consistent fume control effectiveness.
Monitoring and Maintenance
To maintain an effective localized weld fume control system, continuous monitoring and regular maintenance are essential. Incorporate real-time monitoring equipment to assess air quality and ensure that the system is performing optimally. Routine maintenance, such as filter replacements and system cleaning, is crucial for long-term efficiency and worker safety.
Conclusion
Localized weld fume control is a vital component of workplace safety, particularly in industries that rely on welding processes. Effective design considerations encompass understanding fume generation, proper hood design, adequate airflow and ventilation, filtration and treatment systems, system flexibility, and vigilant monitoring and maintenance. By addressing these factors, companies can create a safer and healthier work environment, protecting the well-being of their employees while maintaining productivity and compliance with safety regulations.
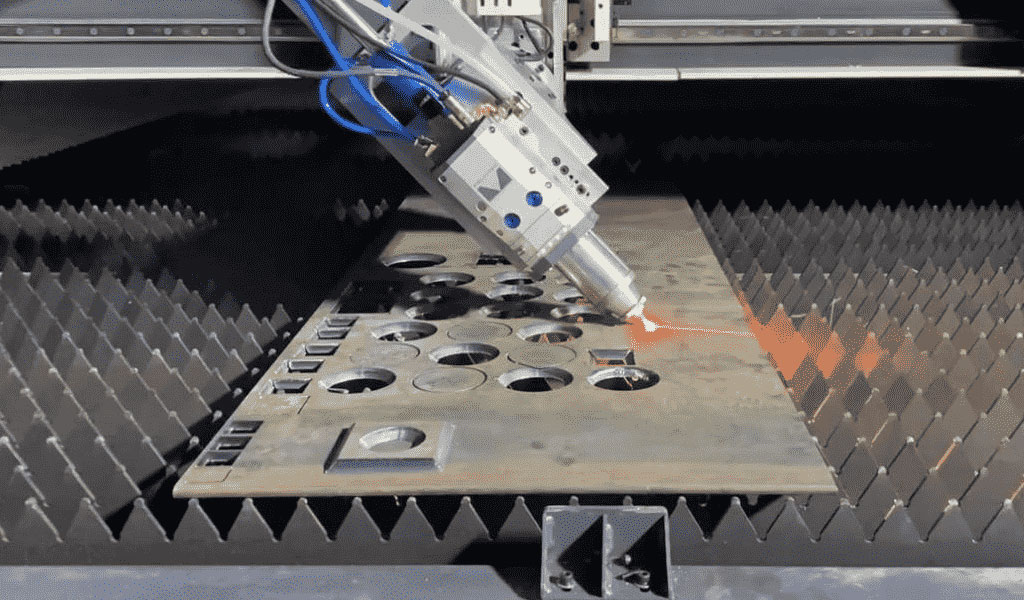
China Sheet Metal Fabrication Manufacturer
Custom precision metal fabrication services. Product specialties include UL® certified NEMA enclosures for various environmental conditions. Capabilities include punching, shearing, laser cutting, bending, machining, press brake forming, and welding. Materials worked with include mild steel, stainless steel, aluminum, brass, and more. Production volumes range from prototype to 10,000 pieces annually. Contract options include discrete orders, blanket orders, quarterly buys, and annual contracts. Value added services include inventory management, rapid prototyping, process development, design for manufacturability, inspection, supply chain management, transportation, and logistics. Industries served include aerospace, automotive, defense, electronic, electrical, entertainment, food and beverage, health, industrial automation, machinery, medical, oil, energy, power, sporting goods, telecommunications, transportation, and more.
using high quality materials
for your sheet metal parts orders
We uses a wide range of material selections for our sheet metal fabrication process. Among our materials are aluminum, stainless steel, brass, magnesium, copper, carbon steel, bronze, galvanized steel, and more. Each material is available in different grades and varieties. Rest assured that all the materials used for your sheet metal parts are durable, corrosion-resistant, long-lasting, rust-proof, wear-resistant, and high-performance. If you want a specific material to be used in the sheet metal fabrication process, don’t hesitate to contact us!
- Carbon Steel
- Stainless Steel
- Aluminum
- Brass
- Copper
- Magnesium
- Bronze
- Galvanized Steel
Why BE-CU is Trusted by 1000+ Clients
Our sheet metal fabrication covers a lot of benefits to many industries, businesses, or projects. Below are the advantages of our services.
- Affordable and Fast Production:We can quickly produce different sheet metal prototypes and final products. KDM offers speedy production while assuring high precision. Our high-volume production also allows us to have cost-effect sheet metal fabrication services.
- Excellent Strength to Weight Ratio:Through our advanced sheet metal fabrication, we can produce sheet metal parts that are lightweight yet durable. We assure high strength, scratch resistance, and corrosion resistance to all produced sheet metal products.
- Wide Range of Materials and Techniques Used:We are experts in different sheet metal fabrication techniques that allow us to produce complex parts with additional intricate features such as notches, slots, holes, etc. Our wide range of sheet metal materials can also withstand electrical, high heat, corrosion, and more.
Online Contact China Precision Sheet Metal Manufacturers
As a direct supplier of precision machined and finished complete components to all segments of the aerospace, semiconductor, automotive, and medical industries, including innovative high tech startups, BE-CU Sheet metal manufacturer is your trusted source for precision sheet metal fabrication services.
To learn more about our aluminum,stainless steel and other steel alloy sheet metal fabrication services, contact us, or give us a call at +86 153 8731 8440, and one of our expert associates will assist you. BE-CU is your trusted source for premium sheet metal fabrication services and metal spinning china manufacturer.