Sheet metal fabrication is a fundamental process in various industries, including manufacturing, construction, and automotive. It involves laser cutting, bending, and assembling sheet metal to create a wide range of products, from enclosures and brackets to complex machinery components. Understanding the cost associated with sheet metal fabrication is crucial for businesses to make informed decisions and maintain profitability. In this article, we will explore the various factors that influence sheet metal fabrication costs and provide a step-by-step guide on how to calculate them effectively.
Factors Affecting Sheet Metal Fabrication Costs
Before delving into the cost calculation process, it’s essential to understand the key factors that can significantly impact the overall cost of sheet metal fabrication.
1. Material Costs
The choice of material is a fundamental cost driver in sheet metal fabrication. Different metals, such as steel, aluminum, and stainless steel, vary in cost and characteristics. The thickness of the metal sheet also plays a significant role in determining the material cost, as thicker sheets generally cost more.
2. Sheet Size and Layout
The size of the sheet metal and the layout of the parts to be fabricated on it can influence material utilization and waste. Efficient nesting of parts on a sheet can reduce material costs, as it minimizes scrap and maximizes the number of parts produced from a single sheet.
3. Design Complexity
Complex designs require more time and precision during fabrication, which can lead to higher labor and equipment costs. Simple shapes and straight cuts are generally less expensive to produce than intricate designs with numerous curves and angles.
4. Tolerance and Quality Requirements
Tight tolerances and high-quality finishing can add to the cost. More precise work demands greater skill and meticulous attention to detail, potentially increasing labor hours and material waste.
5. Volume and Batch Size
The quantity of parts being produced in a single run or batch can affect costs. Economies of scale often apply, where larger production runs lead to lower per-part costs due to optimized machine setup and efficient use of labor.
6. Tooling and Equipment
Specialized tooling or equipment may be required for specific projects, leading to additional expenses. The cost of tooling and machinery maintenance should be factored into the overall cost estimate.
Steps to Calculate Sheet Metal Fabrication Costs
Now that we have a good understanding of the factors that influence sheet metal fabrication costs, let’s explore the step-by-step process of calculating these costs.
Step 1: Gather Project Information
Before you can begin calculating sheet metal fabrication costs, you need a clear understanding of the project’s requirements. This includes the design specifications, material selection, and expected production volume.
Step 2: Material Cost Calculation
Start by estimating the material cost. You’ll need to determine the required sheet size, thickness, and type of material. Most sheet metal suppliers provide price lists for different materials. Multiply the material cost per square foot by the total square footage of the sheet metal required for the project.
Material Cost = (Sheet Size in Square Feet) x (Material Cost per Square Foot)
Step 3: Labor Cost Calculation
Labor costs depend on the complexity of the project, the number of man-hours required, and the wage rate of the workforce. It’s crucial to factor in both direct labor (hands-on fabrication) and indirect labor (e.g., setup and supervision). Determine the hourly wage rate for your labor force and multiply it by the estimated hours required for the project.
Labor Cost = (Direct Labor Hours + Indirect Labor Hours) x Hourly Wage Rate
Step 4: Overhead Costs
Overhead costs include expenses related to equipment maintenance, utilities, rent, and administrative functions. Calculate the percentage of overhead costs relative to labor and material costs, and add this percentage to your overall cost.
Overhead Cost = (Overhead Percentage / 100) x (Labor Cost + Material Cost)
Step 5: Tooling and Equipment Costs
If your project requires specialized tooling or equipment, determine the costs associated with their use. This may include setup fees or rental expenses for specific machinery.
Tooling and Equipment Cost = Sum of all Tooling and Equipment Expenses
Step 6: Quality and Tolerance Costs
For projects with strict quality requirements and tight tolerances, allocate an additional cost based on the complexity and precision needed. This cost can be estimated as a percentage of the total cost.
Quality and Tolerance Cost = (Quality and Tolerance Percentage / 100) x (Labor Cost + Material Cost)
Step 7: Batch Size Adjustment
If you are producing a large batch, consider any cost reductions due to economies of scale. This adjustment can be calculated as a percentage reduction in labor and material costs based on the increased production volume.
Batch Size Adjustment = (Batch Size Percentage / 100) x (Labor Cost + Material Cost)
Step 8: Total Cost Calculation
Add up all the cost components to calculate the total sheet metal fabrication cost.
Total Cost = Material Cost + Labor Cost + Overhead Cost + Tooling and Equipment Cost + Quality and Tolerance Cost – Batch Size Adjustment
Case Study: Calculating Sheet Metal Fabrication Costs
Let’s illustrate the cost calculation process with a hypothetical case study.
Suppose you have a project that requires the fabrication of 1000 stainless steel brackets. The brackets are of moderate complexity with no special tooling requirements. Here are the project details:
- Material: Stainless steel
- Sheet size: 4′ x 8′
- Sheet thickness: 0.125 inches
- Labor rate: $25 per hour
- Overhead rate: 20%
- Quality and tolerance requirements: 5%
- Batch size: 1000 brackets
Material Cost: Material cost per square foot of stainless steel: $10 Material cost = (32 square feet) x ($10 per square foot) = $320
Labor Cost: Direct labor hours: 20 hours Indirect labor hours: 5 hours Labor cost = (20 hours + 5 hours) x ($25 per hour) = $625
Overhead Cost: Overhead cost = (20 / 100) x ($625 + $320) = $189
Tooling and Equipment Cost: No special tooling or equipment is required.
Quality and Tolerance Cost: Quality and tolerance cost = (5 / 100) x ($625 + $320) = $47.25
Batch Size Adjustment: Batch size adjustment = (900 / 100) x ($625 + $320) = $8425
Total Cost: Total cost = $320 + $625 + $189 + $0 + $47.25 – $8425 = $707.50
In this case, the total cost to fabricate 1000 stainless steel brackets is $707.50.
Conclusion
Understanding how to calculate sheet metal fabrication costs is essential for businesses involved in manufacturing and engineering. By considering factors such as material costs, labor expenses, overhead costs, tooling and equipment expenses, quality and tolerance requirements, and batch size adjustments, you can arrive at an accurate cost estimate for your sheet metal fabrication projects. Keep in mind that accuracy is crucial for competitive pricing and maintaining profitability, so thorough cost analysis is a critical aspect of the sheet metal fabrication process.
BE-CU Metal has focused on producing various kinds of Metal Fabrication for almost 30 years. We have become one of the Chinese leading manufacturers in the Sheet Metal Fabrication industry.
Today, BE-CU Metal is one of the top manufacturers of quality Metal Fabrication, Stamping parts which is widely used, such as Metal Fabrication for Aerial Work Platform parts (Boom lift parts, Scissor Lift parts, etc.), Container Homes, Material Handling Equipment, Metal Cabinets, Metal Lockers, Traffic Site Management, Truck Body, Metal Trailer, Metal Enclosures, Casino Gambling Machine, display Rack, Metal Box, Power Control box, Metal Advertising Board, Hand Trucks, Hand Carts, U Boat, Mailboxes, Containerized site accommodation, etc.
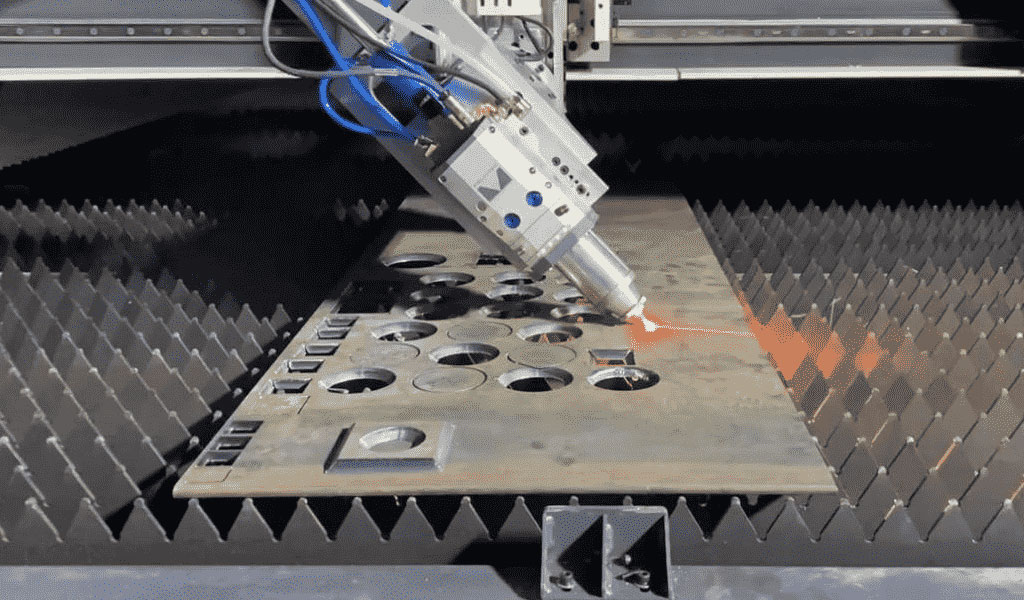
China Sheet Metal Fabrication Manufacturer
Custom precision metal fabrication services. Product specialties include UL® certified NEMA enclosures for various environmental conditions. Capabilities include punching, shearing, laser cutting, bending, machining, press brake forming, and welding. Materials worked with include mild steel, stainless steel, aluminum, brass, and more. Production volumes range from prototype to 10,000 pieces annually. Contract options include discrete orders, blanket orders, quarterly buys, and annual contracts. Value added services include inventory management, rapid prototyping, process development, design for manufacturability, inspection, supply chain management, transportation, and logistics. Industries served include aerospace, automotive, defense, electronic, electrical, entertainment, food and beverage, health, industrial automation, machinery, medical, oil, energy, power, sporting goods, telecommunications, transportation, and more.
using high quality materials
for your sheet metal parts orders
We uses a wide range of material selections for our sheet metal fabrication process. Among our materials are aluminum, stainless steel, brass, magnesium, copper, carbon steel, bronze, galvanized steel, and more. Each material is available in different grades and varieties. Rest assured that all the materials used for your sheet metal parts are durable, corrosion-resistant, long-lasting, rust-proof, wear-resistant, and high-performance. If you want a specific material to be used in the sheet metal fabrication process, don’t hesitate to contact us!
- Carbon Steel
- Stainless Steel
- Aluminum
- Brass
- Copper
- Magnesium
- Bronze
- Galvanized Steel
Why BE-CU is Trusted by 1000+ Clients
Our sheet metal fabrication covers a lot of benefits to many industries, businesses, or projects. Below are the advantages of our services.
- Affordable and Fast Production:We can quickly produce different sheet metal prototypes and final products. KDM offers speedy production while assuring high precision. Our high-volume production also allows us to have cost-effect sheet metal fabrication services.
- Excellent Strength to Weight Ratio:Through our advanced sheet metal fabrication, we can produce sheet metal parts that are lightweight yet durable. We assure high strength, scratch resistance, and corrosion resistance to all produced sheet metal products.
- Wide Range of Materials and Techniques Used:We are experts in different sheet metal fabrication techniques that allow us to produce complex parts with additional intricate features such as notches, slots, holes, etc. Our wide range of sheet metal materials can also withstand electrical, high heat, corrosion, and more.
Online Contact China Precision Sheet Metal Manufacturers
As a direct supplier of precision machined and finished complete components to all segments of the aerospace, semiconductor, automotive, and medical industries, including innovative high tech startups, BE-CU Sheet metal manufacturer is your trusted source for precision sheet metal fabrication services.
To learn more about our aluminum,stainless steel and other steel alloy sheet metal fabrication services, contact us, or give us a call at +86 153 8731 8440, and one of our expert associates will assist you. BE-CU is your trusted source for premium sheet metal fabrication services and metal spinning china manufacturer.