Aluminum, with its remarkable combination of strength, durability, and lightweight properties, is a versatile material used in numerous industries. One of the most popular methods for shaping aluminum into various forms is aluminum extrusion. In this article, we’ll delve into the fascinating world of aluminum extrusion, focusing specifically on aluminum channels. We’ll explore what aluminum channels are, their applications, the extrusion process, and the advantages they offer.
What Are Aluminum Channels?
Aluminum channels, also known as aluminum C-channels, U-channels, or structural channels, are long, straight metal sections with a C or U-shaped cross-section. These channels are created through the aluminum extrusion process, a technique that involves forcing aluminum through a specially designed die to create a desired shape. Aluminum channels come in various sizes, lengths, and thicknesses to suit a wide range of applications.
Applications of Aluminum Channels
- Construction and Architecture: Aluminum channels are frequently used in construction projects for framing windows, doors, and other structural elements. Their lightweight yet robust nature makes them ideal for providing structural support while reducing overall weight.
- Electrical Enclosures: In the electrical industry, aluminum channels are used to create enclosures for various components, providing protection against environmental factors and electrical interference.
- Automotive: Aluminum channels are used in the automotive industry for vehicle body and frame construction, contributing to improved fuel efficiency due to their lightweight properties.
- Manufacturing and Machinery: Aluminum channels are essential in manufacturing, where they serve as structural components in machinery and conveyor systems.
- Transportation: In the aerospace and marine industries, aluminum channels are used for their corrosion-resistant properties and ability to withstand harsh environments.
The Aluminum Extrusion Process
Aluminum extrusion is a manufacturing process that involves shaping aluminum by forcing it through a die with a specific cross-sectional profile. The key steps in the extrusion process are as follows:
- Billet Preparation: Initially, aluminum billets are heated to a temperature where they become malleable.
- Extrusion: The heated aluminum is then forced through a pre-designed die to produce the desired shape, which, in the case of channels, is the C or U-shape.
- Cooling: After extrusion, the aluminum is rapidly cooled to maintain its structural integrity.
- Aging and Cutting: The extruded aluminum is aged to achieve the desired level of hardness and then cut into specific lengths.
Advantages of Aluminum Channels
- Lightweight: Aluminum channels are significantly lighter than their steel counterparts, making them ideal for applications where weight reduction is crucial.
- Corrosion Resistance: Aluminum naturally forms a protective oxide layer, making it highly resistant to corrosion.
- Versatility: Aluminum channels can be easily machined, cut, or welded, allowing for customization to meet specific requirements.
- Sustainability: Aluminum is a highly recyclable material, which makes it an environmentally friendly choice.
- Cost-Effective: The versatility and long lifespan of aluminum channels contribute to cost-effectiveness over time.
Conclusion
Aluminum channels, created through the fascinating process of aluminum extrusion, have a wide range of applications across various industries. Their lightweight, durable, and corrosion-resistant properties make them an attractive choice for structural and framing purposes. As technology and manufacturing processes continue to evolve, aluminum channels are likely to play an even more significant role in shaping the world around us. Whether it’s in construction, manufacturing, or transportation, aluminum channels have proven their worth as an essential component of modern engineering and design.
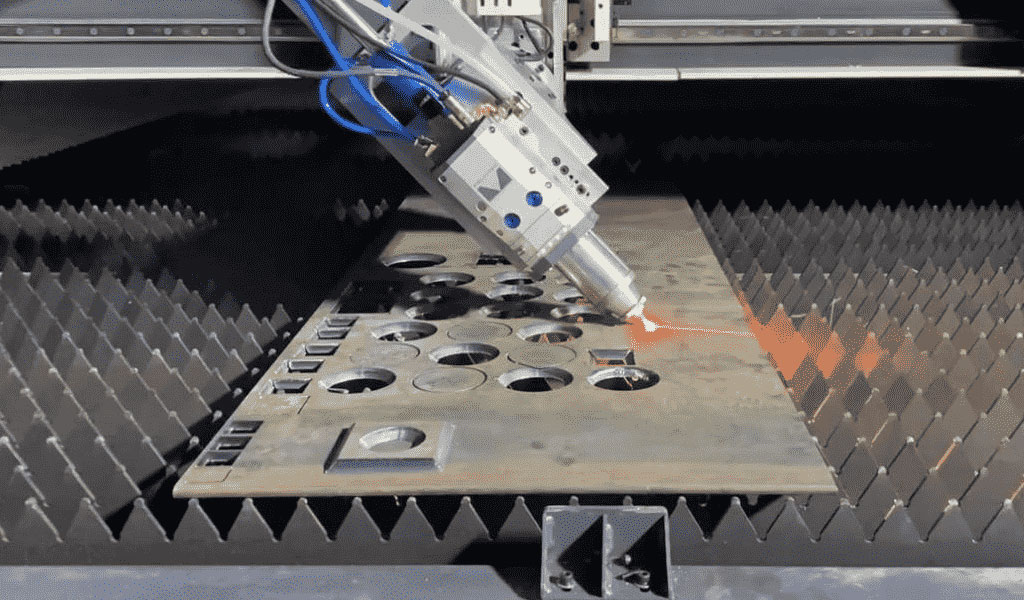
China Sheet Metal Fabrication Manufacturer
Custom precision metal fabrication services. Product specialties include UL® certified NEMA enclosures for various environmental conditions. Capabilities include punching, shearing, laser cutting, bending, machining, press brake forming, and welding. Materials worked with include mild steel, stainless steel, aluminum, brass, and more. Production volumes range from prototype to 10,000 pieces annually. Contract options include discrete orders, blanket orders, quarterly buys, and annual contracts. Value added services include inventory management, rapid prototyping, process development, design for manufacturability, inspection, supply chain management, transportation, and logistics. Industries served include aerospace, automotive, defense, electronic, electrical, entertainment, food and beverage, health, industrial automation, machinery, medical, oil, energy, power, sporting goods, telecommunications, transportation, and more.
using high quality materials
for your sheet metal parts orders
We uses a wide range of material selections for our sheet metal fabrication process. Among our materials are aluminum, stainless steel, brass, magnesium, copper, carbon steel, bronze, galvanized steel, and more. Each material is available in different grades and varieties. Rest assured that all the materials used for your sheet metal parts are durable, corrosion-resistant, long-lasting, rust-proof, wear-resistant, and high-performance. If you want a specific material to be used in the sheet metal fabrication process, don’t hesitate to contact us!
- Carbon Steel
- Stainless Steel
- Aluminum
- Brass
- Copper
- Magnesium
- Bronze
- Galvanized Steel
Why BE-CU is Trusted by 1000+ Clients
Our sheet metal fabrication covers a lot of benefits to many industries, businesses, or projects. Below are the advantages of our services.
- Affordable and Fast Production:We can quickly produce different sheet metal prototypes and final products. KDM offers speedy production while assuring high precision. Our high-volume production also allows us to have cost-effect sheet metal fabrication services.
- Excellent Strength to Weight Ratio:Through our advanced sheet metal fabrication, we can produce sheet metal parts that are lightweight yet durable. We assure high strength, scratch resistance, and corrosion resistance to all produced sheet metal products.
- Wide Range of Materials and Techniques Used:We are experts in different sheet metal fabrication techniques that allow us to produce complex parts with additional intricate features such as notches, slots, holes, etc. Our wide range of sheet metal materials can also withstand electrical, high heat, corrosion, and more.
Online Contact China Precision Sheet Metal Manufacturers
As a direct supplier of precision machined and finished complete components to all segments of the aerospace, semiconductor, automotive, and medical industries, including innovative high tech startups, BE-CU Sheet metal manufacturer is your trusted source for precision sheet metal fabrication services.
To learn more about our aluminum,stainless steel and other steel alloy sheet metal fabrication services, contact us, or give us a call at +86 153 8731 8440, and one of our expert associates will assist you. BE-CU is your trusted source for premium sheet metal fabrication services and metal spinning china manufacturer.