Beryllium bronze, also known as beryllium copper, is a unique copper alloy renowned for its exceptional mechanical properties, including high strength, corrosion resistance, and electrical conductivity. This alloy is commonly used in various industrial applications, including aerospace, electronics, and defense. Two prominent manufacturing processes for working with beryllium bronze are metal spinning and sheet metal forming. While both methods serve to shape and manipulate beryllium bronze, they are distinct in terms of technique, application, and resulting properties. This article aims to compare and contrast beryllium bronze spinning with beryllium bronze sheet metal, exploring their respective advantages, disadvantages, and applications.
Beryllium Bronze: An Overview
Beryllium bronze is an alloy composed primarily of copper with a small percentage of beryllium (typically 0.5% to 3%). The addition of beryllium enhances the material’s strength, hardness, and resistance to fatigue, making it one of the strongest copper-based alloys available. The alloy is also non-magnetic and non-sparking, making it suitable for use in environments where these properties are critical, such as in the manufacturing of tools used in explosive atmospheres.
Metal Spinning: A Traditional Craft
Process Description
Metal spinning, also known simply as spinning, is a metalworking process that involves the shaping of a metal disc or tube by rotating it at high speed on a lathe. As the metal spins, it is pressed against a forming tool or mandrel, gradually conforming to the shape of the tool. The process is often performed manually by skilled artisans or by using automated CNC machines.
Advantages of Beryllium Bronze Spinning
- Complex Shapes: Metal spinning is particularly well-suited for producing axisymmetric shapes, such as cones, cylinders, and hemispheres. The process allows for the creation of intricate geometries that would be challenging or impossible to achieve through other methods.
- Material Efficiency: Spinning can produce parts with minimal waste, as the process involves the deformation of a single metal blank without the need for additional material removal.
- Strength Retention: Beryllium bronze maintains its mechanical properties well during the spinning process, as the process involves work-hardening the material, which can further enhance its strength.
Disadvantages of Beryllium Bronze Spinning
- Labor-Intensive: Traditional metal spinning is highly dependent on the skill of the operator, making it labor-intensive and time-consuming for complex parts.
- Limited to Axisymmetric Parts: The metal cnc spinning process is inherently limited to creating shapes that are symmetrical around an axis, restricting its application to certain types of components.
- Potential for Work-Hardening: While work-hardening can be an advantage, it can also lead to brittleness in the material if not controlled properly during the spinning process.
Beryllium Bronze Sheet Metal: Versatile Fabrication
Process Description
Sheet metal forming is a broad category of manufacturing processes used to shape flat sheets of metal into various forms. Common sheet metal techniques include bending, stamping, deep drawing, and laser cutting. These methods involve the application of force to the sheet, causing it to deform into the desired shape.
Advantages of Beryllium Bronze Sheet Metal
- Versatility: Sheet metal forming techniques can produce a wide variety of shapes, including complex, non-axisymmetric geometries. This versatility makes sheet metal forming suitable for a broad range of applications.
- Scalability: Sheet metal processes, particularly stamping, are highly scalable, making them ideal for mass production. Once the tooling is set up, large quantities of parts can be produced rapidly and with consistent quality.
- Precision: Modern sheet metal techniques, especially those using CNC machines(or using cnc machining china machine), offer high levels of precision, allowing for tight tolerances and intricate designs.
Disadvantages of Beryllium Bronze Sheet Metal
- Material Waste: Sheet metal processes often involve cutting and trimming, which can lead to material waste, especially when producing complex shapes.
- Tooling Costs: The initial cost of tooling for processes like stamping can be high, making it less cost-effective for small production runs.
- Mechanical Properties: Depending on the forming process used, the mechanical properties of the beryllium bronze can be affected. For instance, excessive cold working can lead to undesirable hardening or stress concentration in the material.
Comparative Analysis
Applications
The choice between metal spinning and sheet metal forming often depends on the specific application and desired properties of the final product. Metal spinning is typically preferred for producing axisymmetric parts such as nozzles, domes, and decorative objects, where the strength and seamless nature of the component are critical. In contrast, sheet metal forming is favored for producing parts with complex shapes and designs, such as enclosures, brackets, and chassis used in electronics and aerospace industries.
Production Volume
Metal spinning is generally more suitable for low to medium production volumes, particularly when customized or small-batch production is required. The manual nature of traditional spinning allows for flexibility in design changes without significant additional cost. On the other hand, sheet metal forming, especially when using stamping or deep drawing, is ideal for high-volume production due to its efficiency and repeatability.
Cost Considerations
Cost is a significant factor when choosing between these two processes. Metal spinning, while cost-effective for small batches, can become expensive when large quantities are needed due to the manual labor involved. Conversely, sheet metal forming, with its higher initial tooling costs, becomes more economical as production volume increases.
Material Utilization
Both processes have their strengths in material utilization. Metal spinning tends to have less material waste, as it primarily involves deformation rather than cutting. However, sheet metal processes, despite potentially higher waste, offer more flexibility in material thickness and type, allowing for tailored solutions based on the application.
Conclusion
Beryllium bronze spinning and sheet metal forming are both valuable manufacturing processes, each with its distinct advantages and applications. The choice between them depends on factors such as the complexity of the desired shape, production volume, cost considerations, and the specific mechanical properties required. By understanding the strengths and limitations of each process, manufacturers can select the most appropriate method to meet their needs, ensuring the production of high-quality beryllium bronze components that meet the demands of their respective industries.
In conclusion, while metal spinning service offers efficiency and strength retention for axisymmetric parts, sheet metal forming provides versatility and precision for complex shapes, making both processes indispensable in the realm of beryllium bronze manufacturing.
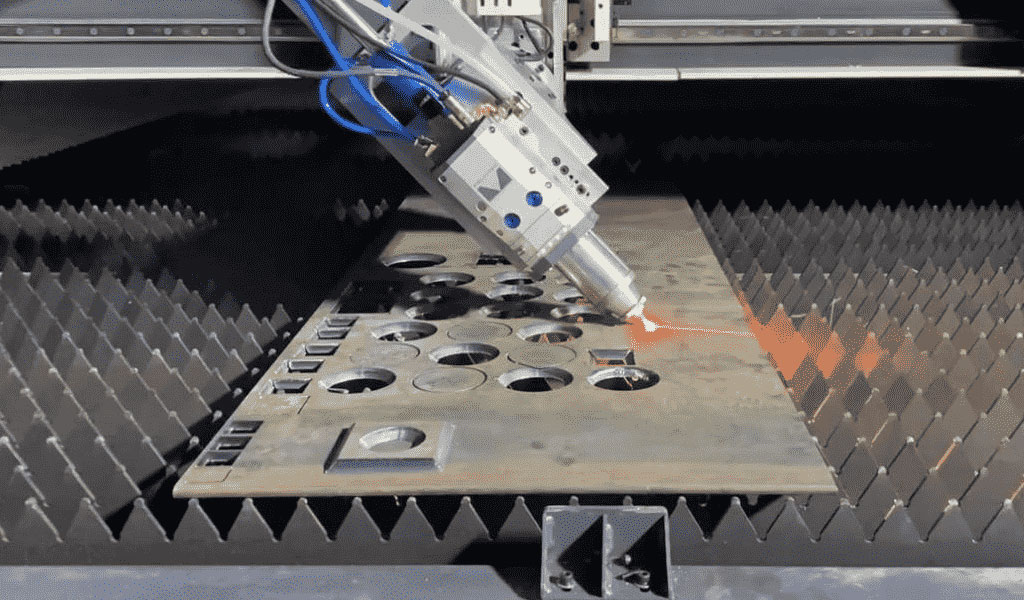
China Sheet Metal Fabrication Manufacturer
Custom precision metal fabrication services. Product specialties include UL® certified NEMA enclosures for various environmental conditions. Capabilities include punching, shearing, laser cutting, bending, machining, press brake forming, and welding. Materials worked with include mild steel, stainless steel, aluminum, brass, and more. Production volumes range from prototype to 10,000 pieces annually. Contract options include discrete orders, blanket orders, quarterly buys, and annual contracts. Value added services include inventory management, rapid prototyping, process development, design for manufacturability, inspection, supply chain management, transportation, and logistics. Industries served include aerospace, automotive, defense, electronic, electrical, entertainment, food and beverage, health, industrial automation, machinery, medical, oil, energy, power, sporting goods, telecommunications, transportation, and more.
using high quality materials
for your sheet metal parts orders
We uses a wide range of material selections for our sheet metal fabrication process. Among our materials are aluminum, stainless steel, brass, magnesium, copper, carbon steel, bronze, galvanized steel, and more. Each material is available in different grades and varieties. Rest assured that all the materials used for your sheet metal parts are durable, corrosion-resistant, long-lasting, rust-proof, wear-resistant, and high-performance. If you want a specific material to be used in the sheet metal fabrication process, don’t hesitate to contact us!
- Carbon Steel
- Stainless Steel
- Aluminum
- Brass
- Copper
- Magnesium
- Bronze
- Galvanized Steel
Why BE-CU is Trusted by 1000+ Clients
Our sheet metal fabrication covers a lot of benefits to many industries, businesses, or projects. Below are the advantages of our services.
- Affordable and Fast Production:We can quickly produce different sheet metal prototypes and final products. KDM offers speedy production while assuring high precision. Our high-volume production also allows us to have cost-effect sheet metal fabrication services.
- Excellent Strength to Weight Ratio:Through our advanced sheet metal fabrication, we can produce sheet metal parts that are lightweight yet durable. We assure high strength, scratch resistance, and corrosion resistance to all produced sheet metal products.
- Wide Range of Materials and Techniques Used:We are experts in different sheet metal fabrication techniques that allow us to produce complex parts with additional intricate features such as notches, slots, holes, etc. Our wide range of sheet metal materials can also withstand electrical, high heat, corrosion, and more.
Online Contact China Precision Sheet Metal Manufacturers
As a direct supplier of precision machined and finished complete components to all segments of the aerospace, semiconductor, automotive, and medical industries, including innovative high tech startups, BE-CU Sheet metal manufacturer is your trusted source for precision sheet metal fabrication services.
To learn more about our aluminum,stainless steel and other steel alloy sheet metal fabrication services, contact us, or give us a call at +86 153 8731 8440, and one of our expert associates will assist you. BE-CU is your trusted source for premium sheet metal fabrication services and metal spinning china manufacturer.